А. Н. Орберг, В. В. Виноградов, А. М. Панкратов, В. Б. Сударев – ЗАО «ОРМА»
Резкий рост цен на энергоносители заставляет компании, эксплуатирующие энергетическое оборудование, искать способы повышения его экономичности. Особенно это актуально для газотранспортных предприятий, где с увеличением объемов перекачиваемого природного газа растут и затраты на собственные нужды. Существенные расходы газа, используемого в качестве топлива, – следствие низкой экономичности применяемого оборудования, что связано в значительной степени с его моральным и физическим износом. Ремонт или замена ряда критических узлов широко распространенного газоперекачивающего агрегата ГТК-10-4: регенератора, камеры сгорания, внутренней вставки корпуса, обоймы турбины – существенно продлевает его назначенный ресурс, а уcтановка утилизатора-водоподогревателя заметно повышает экономичность агрегата в целом.
Добыча природного газа в России с 2001 года неуклонно растет. По объему экспорта природного газа страна занимает первое место в мире. Более трех тысяч газотурбинных агрегатов (ГПА) общей установленной мощностью около 40 млн кВт обслуживают протяженную газотранспортную сеть страны.
Значительная часть этих агрегатов уже выработала свой назначенный ресурс. Это сотни газотурбинных установок (ГТУ), характеристики которых могут быть восстановлены за счет модернизации и качественного ремонта. При сравнительно небольших затратах можно в короткие сроки вернуть в строй ГТУ c основными показателями, даже превышающими паспортные значения.
В первую очередь это относится к таким газоперекачивающим агрегатам сети компрессорных станций, как ГТК-10-4 и ГТ-750-6. Одна из основных причин снижения характеристик (КПД, мощность) этих ГПА – разрушение теплообменной матрицы пластинчатых регенераторов. Учитывая, что большое количество таких газотурбинных установок все еще находится в эксплуатации (около 600 агрегатов), решение этой проблемы имеет особое значение.
Трубчатый воздухоподогреватель стал удачным решением эффективной замены дефектных пластинчатых регенераторов. Важным преимуществом типового ряда регенераторов, разработанных и изготавливаемых ЗАО «ОРМА», (помимо их уникальных возможностей по восстановлению показателей эффективности ГПА и снижению расхода природного газа на собственные нужды) является возможность их доставки без использования спецтехники и быстрый монтаж на старом фундаменте (фото 1). Уменьшение металлоемкости, а также повышение надежности способствовали широкому внедрению таких регенераторов. Только за последние три года на компрессорных станциях ОАО «Газпром» введено в эксплуатацию более 80 регенераторов этого типа.
Кроме того, модульность и простота конструкции позволяют организовать производство по конвейерному принципу, что ведет к снижению себестоимости регенераторов. Это особенно важно при проведении мероприятий по продлению ресурса именно изношенного оборудования. Проверенные и отработанные в серийном производстве трубчатые воздухоподогреватели имеют резервы для дальнейшего совершенствования и повышения степени регенерации за счет использования апробированных методов интенсификации теплообмена.
Требования к экологической безопасности энергетического оборудования постоянно ужесточаются, и удовлетворение их порой даже превалирует над достижением высокой экономичности. Физический износ ГПА неизбежно приводит к значительному росту количества вредных выбросов, в частности NOх. Комплексная модернизация или замена камеры сгорания (КС) существенно улучшает экологические характеристики агрегатов. ЗАО «ОРМА» проводит такую модернизацию. В ее основе лежит рациональная подача воздуха в зону горения КС, за счет чего подавляются высокотемпературные очаги, снижая образование NOх в продуктах сгорания. Эффективность этого метода, простота конструкции и надежность изготавливаемых низкотоксичных КС (фото 2) способствовали существенному увеличению объема заказов в 2005 г.
Важным элементом ГТК-10-4 и ГТ-750-6 является внутренний жаропрочный корпус турбины (вставка) – тонкостенная разъемная оболочка сложной конфигурации (фото 3), находящаяся под непосредственным воздействием высокотемпературного газового потока и от состояния которой зависит работоспособность всего агрегата в целом. В 2004 году КБ ЗАО «ОРМА» разработало более термопластичную конструкцию внутренного корпуса для ГТК-10-4. В короткие сроки была изготовлена сложная технологическая оснастка (штампы) и организовано серийное производство вставок. Использование разработанной технологии уже применительно к вставкам для агрегатов ГТ-750-6, наладка их производства и ритмичная поставка этих важных элементов позволят в условиях компрессорных станций выполнить ремонт и ввести в действие агрегаты, значительная часть которых в настоящее время простаивает.
Ощутимо повысить эффективность использования топлива можно за счет внедрения в схему ГПА утилизационного теплообменника (УТО), каждая секция которого монтируется на участке газохода между регенератором и дымовой трубой. Горячая вода УТО используется в технологических целях и для отопления цехов коспрессорных станций, а также в системе теплофикации жилого района.
Теплообменник УТО-2,5, созданный ЗАО «ОРМА», предназначен для газотурбинного привода с длительной наработкой. При небольших габаритах он обладает высокой тепловой мощностью, малым аэродинамическим сопротивлением газового тракта, широким диапазоном регулирования теплопроизводительности. Блочная поставка заметно сокращает время монтажа. Такие теплообменники уже работают в составе ГПА на компрессорных станциях России.
Разработанный ряд УТО совершенствуется: проводятся мероприятия по увеличению эффективности использования бросового тепла за счет поднятия единичной теплопроизводительности УТО, по расширению диапазона регулирования, повышению ремонтопригодности и внедрению автоматизации управления.
Накопленный опыт в разработке, изготовлении, монтаже отдельных элементов и узлов модернизируемых ГПА, их надежная эксплуатация на компрессорных станциях позволили существенно расширить объемы выполняемых работ и приступить к комплексному ремонту всего турбоблока типа ГТК-10-4 (фото 4). Он включает полную разборку и дефектацию всех узлов и деталей, их восстановление, модернизацию или замену (в случае неремонтопригодности), а также стендовую сборку агрегата и проведение теплотехнических испытаний при сдаче заказчику. 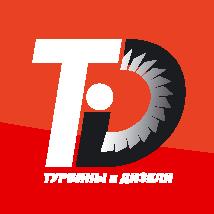