А. А. Никитин – представительство Wartsila, Москва
Веса Риихимяки, Никлас Хага, Грегор Колль – Wartsila, Финляндия
Корпорация Wartsila, признанный лидер в производстве среднеи низкооборотных дизельных, газовых и двухтопливных двигателей и различных станций на их основе, постоянно совершенствует свою технологию. Она имеет большой опыт работы с международными нефтяными и газовыми компаниями. В статье рассказывается о возможностях работы двигателей на нескольких видах топлива при выработке электрической и тепловой энергии на нефтяных и газовых месторождениях, а также об утилизации отходов нефтепереработки.
Газодизельные технологии – система «топливные доли»
Сегодня рынок производства энергии требует разнообразных технических решений, которые могли бы удовлетворять потребности заказчика в каждом сегменте рынка. Корпорация Wartsila предлагает несколько типов газовых технологий, отвечающих различным потребностям. Самая последняя разработка – технология «топливные доли» – успешно применяется там, где топливом является попутный нефтяной газ и отходы нефтепереработки.
Газодизельная технология (GD) была разработана в 1987 вместе с двигателем Wartsila 32GD – первым газовым двигателем в программе корпорации Wartsila. Эта технология применялась, в основном, на морских платформах, но использовалась также и в наземной энергетике. Газодизельная технология позволяет электростанции работать как на газообразном, так и на жидком (тяжелом или легком) нефтяном топливе. Преимущество многотопливной системы проявлялось, прежде всего, в отсутствии зависимости от поставок топливного газа. Кроме того, газодизели нечувствительны к изменению качества газа.
При работе в газодизельном режиме впрыскивается небольшое количество жидкого топлива для воспламенения. Наличие газового компрессора для впрыска газа под высоким давлением часто рассматривается как дополнительные инвестиции для электростанции традиционного назначения.
С 1993 года начала применяться новая технология – с использованием обедненных газовых смесей с искровым зажиганием (SG). Она была представлена двигателем Wartsila 25SG, а затем Wartsila 34SG. Технология SG разработана специально для энергетической отрасли, когда можно снизить инвестиционные затраты при наличии надежных поставок газа хорошего качества. В связи с этим двигатели Wartsila с искровым зажиганием стали самыми востребованными в производственной программе корпорации.
Технология SG была позднее трансформирована в двухтопливную технологию (DF), которая отличалась большей гибкостью. В DF-системах обедненная газовая смесь воспламеняется небольшим количеством пилотного легкого жидкого топлива, поэтому свечи для такого двигателя не нужны. Кроме того, двухтопливные двигатели включают обычную топливную систему для работы на дизельном топливе.
Данные технологии были разработаны для удовлетворения потребностей энергетического рынка, а также для индивидуальных заказчиков. Дальнейшее развитие газодизельной технологии – система «топливные доли». Она предназначена, в основном, для применения на нефтяных месторождениях, а также в связанных с нефтегазовой отраслью технологических процессах.
Топливные доли – это система топливосмешения, позволяющая двигателю работать на газе и жидком топливе в различных пропорциях. Она применяется для того, чтобы оптимизировать эксплуатацию электростанций исходя из наличия топлива. Например, если газа имеется только 30% от количества топлива, необходимого для достижения заданной мощности, то двигатель будет использовать на оставшиеся 70% жидкое топливо. Оператор может легко менять уставку топливных долей, а система управления будет поддерживать фактическую рабочую точку в пределах рабочих окон. Оператор может также установить обычный газодизельный или жидкотопливный режим работы двигателя. Для того чтобы иметь представление о рабочем окне топливных долей, нужно рассмотреть каждую рабочую область отдельно (рис. 1).
Жидкотопливный режим
Работа на жидком топливе основана на использовании обычных инжекционных топливных насосов, а установка работает как любой дизельный двигатель. Она может работать, например, на дизельном топливе, мазуте или нефти как основном топливе (и как пилотном) без каких-либо изменений в топливной системе. Работа на жидком топливе возможна во всем диапазоне нагрузок – от нуля до номинала.
Газодизельный режим (GD)
Основным источником энергии при таком режиме является газ, хотя в двигатель постоянно подается для воспламенения примерно 5% пилотного топлива. Газодизельный режим доступен в диапазоне 30…100% номинальной мощности двигателя, а переход с GD-режима на жидкотопливный (и наоборот) возможен в диапазоне 30…87% мощности двигателя.
Режим топливных долей
Этот режим работы возможен в диапазоне мощности от 30 до 100%. Рабочая точка топливных долей может быть задана с системы интерфейса оператора Wartsila (WOIS). Например, необходимо, чтобы доля газа от всего сжигаемого в двигателе топлива составляла 30 % на полной нагрузке. Для этого рабочая точка устанавливается на значение 30%, и выбирается режим работы «топливные доли».
Если в какой-то момент нагрузка двигателя слишком мала, то система управления будет автоматически настраивать рабочую точку в соответствии с минимальной или максимальной границей. Если нагрузка вернется на уровень,
когда может быть достигнуто заданное 30-процентное значение, то система управления вернет двигатель к работе на заданных топливных долях. Оператор может изменить уставку в любой момент работы двигателя.
Для обеспечения безопасной эксплуатации область работы в режиме топливных долей ограничена определенным окном. На рис. 1 отмечены граничные точки топливных долей:
1. Минимальная доля газа – 15% мощности на полной нагрузке. Это фиксированная граница, которая определяется минимально возможным объемом впрыскиваемого газа. Следовательно, когда нагрузка снижается, нижняя граница пропорционально повышается (больше процентная доля газа). Минимальная доля газа определяется для обеспечения надежной работы газовыпускного клапана.
2. Максимальная доля газа в режиме топливных долей составляет примерно 80% при нагрузке двигателя 87,5% от номинала. Непрерывная работа между газодизельным режимом и выше этой границы не разрешается, поскольку характеристика жидкотопливного насоса имеет инверсионную область между кривыми подачи основного и пилотного топлива. Инверсионная работа означает, что подъем рейки топливного насоса приводит к снижению расхода топлива. Эта зона «проходится» за один шаг при переходе в газодизельный режим работы.
3. Минимальная мощность двигателя в режиме топливных долей – 35% от номинала. Это точка, где пересекаются границы минимального и максимального значения топливных долей. Если нагрузка двигателя менее 35%, то система управления автоматически переведет его в жидкотопливный режим работы. Переключение выполняется как быстрый переход, а не как отсечение газа. Это означает, что газотопливная система в течение некоторого времени сохраняется в состоянии готовности, чтобы иметь возможность совершить быстрый обратный переход в режим топливных долей, когда нагрузка двигателя вернется к уровню более 35%.
Реальное значение топливных долей определяется положениями соленоида исполнительного механизма. Для достижения нужного значения АСУ обрабатывает линеаризованные сигналы механизмов, которые откалиброваны в соответствии с условиями окружающей среды и свойствами располагаемого топлива. Если теплотворная способность топлива не меняется, точность работы системы в этом случае – выше. Вместе с тем, система допускает и некоторые изменения, но они не вызывают каких-либо проблем с эксплуатацией.
Технология топливных долей
Система топливных долей – это, по сути, комбинация газодизеля и новой автоматизированной системы управления. Она одновременно управляет как подачей газа, так и жидкого топлива, позволяя использовать оба вида топлива одновременно в границах разрешенных рабочих окон. Новая АСУ полностью интегрирована в программируемый контроллер (PLC) системы управления верхнего уровня, основанной на стандартной платформе Wartsila.
АСУ системы топливных долей состоит из нескольких контуров управления, которые работают под одним центральным процессором (CPU). Конфигурация системы управления оборотами и подачей газа показана на рис. 2. Обороты и нагрузка двигателя управляются специальным PID-контроллером, встроенным в программу главного PLC. Контроллер оборотов предоставляет много различных оптимизированных способов управления.
Управление количеством газа и жидкого топлива осуществляется специальным контроллером двухтопливного актюатора, который также встроен в программу PLC. Он получает общий сигнал управления от PID-контроллера оборотов и распределяет его на два актюатора в соответствии с заданными уставками и эксплуатационными условиями.
Сигналы управления PLC соединены с исполнительными механизмами, которые передают общие сигналы управления двум контурам топливоподачи для каждого цилиндра с откорректированными параметрами.
Жидкотопливный регулятор – электрогидравлический (как и в обычном дизельном двигателе). Газотопливный регулятор представляет собой электронную систему EVR (Electronic Valve Rail), которая управляет специальными инжекционными клапанами.
В дополнение к функциям двухприводного актюатора, встроенные сигналы включают управление давлением топливного газа, которое поддерживается в пределах 25…35 МПа (в зависимости от уровня газоподачи). При сжигании небольшого количества газа (низкая топливная доля газа или низкая мощность двигателя) обеспечивается пониженное давление газа для увеличения продолжительности впрыска топлива.
Управление давлением уплотняющего масла высокого давления интегрировано в систему управления давлением газа, при этом поддерживается уровень, при котором давление уплотняющего масла на 2 МПа выше давления газа.
И, наконец, немаловажная особенность: система объединяет функции определения последовательности работы газовых клапанов и безопасности. Не вдаваясь в детали относительно этой последовательности, отметим следующие функции газовых клапанов:
а) в случае необходимости сдвоенные основные газовые клапаны обеспечивают отсечение подачи газа от двигателя;
б) медленное заполнение системы во время запуска: газовый тракт заполняется через байпасную линию, чтобы избежать внезапных колебаний давления в системе;
в) система продувки используется для рециркуляции сжатого газа на стороне всасывания газового компрессора, когда прекращается подача газа в двигатель;
г) сдвоенные вентиляционные клапаны применяются для сжигания отвода остатков газа в газовом тракте после продувки;
д) газовая система безопасности отключает и отсекает подачу газа в двигатель.
Применение технологии
Технология топливных долей была впервые испытана в 1999 году на двигателе Wartsila 4R32GD для танкера сжиженного газа. Испытания, которые выполнялись «вручную», показали, что система работает, однако на тот момент она не была универсальной.
В 2002 году к корпорации Wartsila обратилась с заказом эквадорская компания Dygoil, которой нужна была электростанция для нефтяного месторождения. Основное требование, предъявляемое к станции: она должна была работать как на попутном газе, так и на нефти, поскольку поставки природного газа были нестабильны, а объемы попутного нефтяного газа уменьшались по мере увеличения обводненности пластов.
Эти требования могли быть обеспечены только возможностями системы топливных долей. За очень короткий срок корпорацией была разработана система топливных долей для двух дизель-генераторных установок Wartsila 16V32LNGD (фото 1). Электростанция была введена в эксплуатацию в марте 2004 года.
Проект Dygoil наилучшим образом демонстрирует рыночную нишу для применения технологии топливных долей. Но возможности этой технологии не ограничиваются лишь указанным применением. Топливная система может быть использована как для газов с очень низким метановым числом, так и для газов, имеющих очень низкую теплотворную способность (в режимах «топливные доли» и, частично, в газодизельном режиме).
Поскольку технология топливных долей позволяет объединять различные виды топлива, это делает ее в определенных случаях наиболее экономически оправданной. С того времени как система управления топливными долями была интегрирована в стандартную АСУ Wartsila, ее применение в случае имеющихся (или будущих) изменений объема и качества газа стало более привлекательным, чем обычная газодизельная система.
Основные достоинства системы топливных долей:
а) гибкость эксплуатации при различных соотношениях газа и жидкого топлива;
б) возможность использования различных видов жидкого топлива, например дизельного, мазута и нефти в качестве основного и пилотного топлива;
в) возможность работы на попутном нефтяном газе с низким метановым числом;
г) способность системы сжигать низкокалорийные газы.
Использование отходов нефтеперегонки в качестве топлива
За прошедшие 10 лет перечень видов топлива, которые могут использоваться для дизельных двигателей корпорации Wartsila, значительно увеличился. Например, недавно поставленные в Мексику электростанции успешно эксплуатируются на отходах нефтеперегонки, отличающихся высокой вязкостью.
Традиционно двигатели Wartsila работали на легком дизельном топливе, а с 1970 года – на тяжелых видах топлива. С конца 1990-х годов началась эксплуатация оборудования на сырой нефти и биотопливе, оримульсии (жидкое топливо на основе битума), отходах при перегонке нефти. В результате в настоящее время уже поставлено энергетическое оборудование общей мощностью свыше 1000 МВт для работы на нестандартных видах топлива.
Принимая во внимание, что затраты на топливо составляют 60…70% от общих эксплуатационных расходов дизельных электростанций, владельцы оборудования, естественно, стремятся снизить затраты на него. При этом стоимость отходов нефтеперегонки в несколько раз ниже, чем других видов топлива.
Состав отходов во многом зависит от качества сырой нефти и от самого процесса перегонки. При сложном многоступенчатом процессе отходы имеют более низкую теплотворную способность, чем при простой перегонке.
На нефтеперегонных заводах чаще всего используется многоступенчатый технологический процесс с целью максимального получения продуктов перегонки – бензина, авиационного керосина и дизельного топлива. Технологический процесс включает в себя вакуумную перегонку, термический крекинг, каталитический крекинг и этап понижения вязкости. В результате образуются отходы, обладающие высокой степенью вязкости, например битум. Затем к отходам добавляется какой-либо компонент, который обеспечивает снижение вязкости и дает возможность использовать их в качестве топлива. При этом данный компонент добавляется в возможно малых количествах с целью поддержания цены топлива на низком уровне. Определение цены на данный продукт индивидуально для каждого отдельного нефтеперерабатывающего завода.
Оценка качества полученного топлива
При оценке качества нестандартных видов топлива необходим его полный и достоверный лабораторный анализ в дополнение к спецификации продукции, которая чаще всего не полностью отражает его состав. Анализ топлива должен включать в себя информацию по следующим позициям:
1. Вязкость. Для двигателей Wartsila вязкость топлива не должна превышать 16…24 cСт в точке впрыска. Это необходимо для достижения оптимального распыления с целью поддержания нормального процесса горения. Слишком высокая вязкость топлива приведет к повышенному механическому давлению на впрыске, а слишком низкая – к недостаточному давлению и недостаточной смазке топливной форсунки. Стандартные тяжелые виды топлива с вязкостью 700 cСт при температуре 50 °С требуют предварительного подогрева до 130…135 °С перед впрыском. Если топливо имеет большую вязкость, то его необходимо предварительно подогревать до более высокой температуры. Ранее проблемой являлось то обстоятельство, что компоненты топливной системы и уплотнения из стандартных материалов не выдерживали высоких температур, и их срок службы в связи с этим резко сокращался. В настоящее время разработаны материалы, которые обеспечивают надежную работу при температуре топлива 150 °С. В связи с этим для двигателей могут использоваться виды топлива, имеющие вязкость 2500…3000 cСт (50 °С).
2. Особенности зажигания. Индекс CCAI (Calculated Carbon Aromaticity Index) – ISO 8217 – основан на формуле расчетов, которые дают приблизительную характеристику особенностей воспламенения данного вида топлива. Если этот индекс будет иметь значение выше 870, то могут возникнуть сложности с воспламенением топлива.
3. Плотность. Современные центробежные сепараторы могут обрабатывать топливо плотностью до 1010 мг/м3 при температуре 15 °С. Если плотность превышает данное значение, воду из топлива удалить невозможно.
4. Вода. Максимальное сдержание – 1 % от объема топлива в условиях хранения и 0,3 % – после его подготовки. В центробежном сепараторе содержание воды должно быть ниже 0,3 % от объема топлива до впрыска в камеру сгорания, поскольку примеси, растворенные в воде, способствуют разрушению компонентов двигателя.
5. Углеродный остаток. Максимальное содержание – 22 %. Наличие в топливе углеродных примесей приводит к образованию при высоких температурах углеродных отложений в камере сгорания и выхлопной системе, особенно при работе двигателя с низкими нагрузками.
6. Битумы. Максимальное содержание не более 14 % от объема. Наличие в топливе битумов также способствует образованию отложений в камере сгорания и в выхлопной системе двигателя. Битумы приводят также к забиванию фильтров и образованию осадка в топливных баках и сепараторах.
7. Зола. Ее содержание не должно превышать 0,2 %. Анализ состава золы показывает присутствие в ней различных загрязнителей и примесей, таких как песок и пыль, а также ванадия, соды, никеля, кремния, железа, кальция и магния. Некоторые элементы, например ванадий и никель, невозможно удалить из топлива с помощью обычного сепаратора. При этом возникают такие проблемы, как быстрый износ компонентов системы впрыска, поршней и цилиндров; загрязнение компонентов двигателя и турбокомпрессора; горячая коррозия компонентов двигателя; прогорание клапанов и поршней.
8. Ванадий и сода. Максимальное содержание ванадия – 600 мг/кг, а соды – 100 мг/кг при хранении и 30 мг/кг после подготовки топлива. Оксиды ванадия и соды образуются в процессе горения, затем они соединяются с другими примесями – никелем, кальцием и серой, что в результате приводит к загрязнению компонентов двигателя, горячей коррозии и перегреву двигателя.
9. Алюминий и кремний. Максимальное содержание – 80 мг/кг при хранении и 15 мг/кг после подготовки топлива. Данные примеси очень агрессивны и обладают сильным абразивным эффектом. Значительное их содержание приводит к быстрому износу компонентов двигателя, системы впрыска, топливных форсунок цилиндров поршней и т.д. Для удаления примесей из топлива используют высокоэффективные сепараторы.
10. Осадок. Максимальное содержание – 0,1% от общей массы топлива. Наличие осадка свидетельствует о присутствии в составе топлива таких примесей, как песок и пыль. В результате отложения примесей происходит закупорка топливных фильтров.
11. Текучесть. Температура потери текучести топлива – минус 30 °С. Для того чтобы избежать потери текучести, температура во всей топливной системе (включая трубопроводы и цистерны) должна быть минимум на 10…15 °С выше точки потери текучести.
12. Воспламенение. Температура воспламенения топлива должна быть не менее 60 °С. Хотя данный параметр и не влияет на процесс горения, но при низкой температуре воспламенения существует опасность возникновения пожара, что требует особой осторожности при работе.
Применение технологии
Последние электростанции, работающие на отходах нефтепереработки, были введены в эксплуатацию в Мексике – в г.г. Пондероса и Пронал. В состав электростанции Ponderosa мощностью 19,39 МВт входят три энергоблока Wartsila 18V32 (фото 2). Электростанция Pronal мощностью 12,68 МВт состоит из двух аналогичных установок.
Обе электростанции запущены в эксплуатацию в июле-августе 2005 года и работают на отходах нефтеперегонного завода Miguel Hidalgo в условиях высокогорья (1900 м над уровнем моря). Топливная система установок специально создана для работы с вязкими видами топлива (вязкость 1100 cСт при температуре 50 °С). Компоненты системы выполнены из термостойких материалов для эксплуатации при высоких температурах. 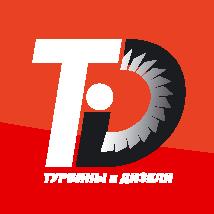