С. Ю. Гаврилов – АК «Якутскэнерго»
П. Е. Кычкин – ОАО «Сахаэнерго»
Себестоимость производства электроэнергии в отдаленных городах и поселках Якутии, в связи с дороговизной завозимого дизельного топлива, достаточно велика. Энергетика таких районов дотационная, и это не дает возможности развиваться удаленным от энергосистемы поселкам. Предприятия-поставщики электроэнергии вынуждены вводить режим экономии топлива и энергопотребления.
При этом в Якутии имеется более дешевое местное топливо – уголь, месторождения которого простираются от южных улусов до берегов Северного моря. Все северные улусы имеют очень сложную транспортную схему – это затрудняет доставку нефтепродуктов. Обычно они доставляются морским или железнодорожным путем и до открытия зимних дорог хранятся на перевалочных базах. С точки зрения экономики, это очень затратный способ.
Поэтому при формировании региональной энергетической политики большое значение имеет применение местных видов топлива. Один из вариантов – газификация относительно дешевых видов угля и использование полученного синтез-газа в качестве топлива для газодизельных и газопоршневых двигателей, а также паровых котлов.
Экономический эффект использования угля в качестве топлива
Средняя цена дизтоплива в Якутии составляет 33000 р./т без транспортных расходов, а сырой нефти – 9045 р./т (для справки: на мировом рынке один баррель сырой нефти – 159 л стоит $90, т.е. 20000 р./т). Причем средняя стоимость дизельного топлива в местах нахождения ДЭС составляет около 40000 р./т.
В то же время в регионе имеются большие запасы более дешевых топлив: это каменный и бурый уголь, сланцы, богхеды (сапрогумолитовый уголь). Приведем общие расчеты перевода всех ДЭС, например, на уголь. Калорийность дизельного топлива составляет 11000…13000 ккал/кг, а калорийность угля – от 5600 до 7500 ккал/кг. Стоимость угля с транспортными расходами 3000…8000 р./т, а дизельного топлива 30000…45000 р./т (при перспективе дальнейшего роста). На производство 1 кал энергии потребуется угля в 2–3 раза больше, однако стоимость произведенной энергии в 5–10 раз ниже, чем при использовании дизельного топлива. Чтобы заменить 100 тыс. т дизтоплива потребуется 300 тыс. т угля.
Конечно, в этих расчетах надо учитывать и способы сжигания угля. Прямое сжигание в котлах предусматривает использование парового цикла, электрический КПД паропоршневой машины не более 10 %, а паровой турбины – 30…35 % (мощностью менее 10 МВт – до 20 %). Газификация твердых топлив – это предварительное сжигание топлива с недостатком окислителя (кислорода) и получением горючего газа (синтез-газа).
Запасы угля в Якутии и его характеристики
Республика располагает 14,4 млрд тонн балансовых запасов угля (по категориям А+В+С1+С2), что составляет 48 % всех запасов Дальневосточного региона. На ее территории находится 48 месторождений, объединяющих 81 участок, – это Ленский, ЮжноЯкутский и Зырянский бассейны, восточная часть Тунгусского бассейна, а также другие разрозненные месторождения.
Состав каменного угля колеблется в широких пределах в зависимости от месторождения. Невысокое содержание летучих веществ позволяет газифицировать каменный уголь так же, как и антрацит, – по прямому процессу, с паровоздушным дутьем. В процессе газификации необходимо учитывать температуру плавления золы данного вида угля. Зольность отдельных видов углей может достигать 20 %. Теплотворная способность каменного угля составляет 6000…7000 ккал/кг.
Бурый уголь, как правило, содержит большое количество золы, достигающее 30 %. Наличие в бурых углях летучих соединений и водорода обусловливает газификацию бурого угля по обращенному процессу, с воздушным или паровоздушным дутьем. Теплотворная способность бурого угля составляет 4000…6000 ккал/кг.
Температура плавления золы влияет на образование флюсов в зоне горения и залипание их на стенки, что отрицательно сказывается на рабочем процессе. На качество синтез-газа, подаваемого в двигатель, негативно влияет и содержание серы – в этом случае требуется дополнительная очистка.
Отличными характеристиками для газификации углей обладает богхед. Его разведанные запасы, расположенные в прибрежных северных районах Якутии, составляют более 1 млн м3. (В свое время, по рассказам местных жителей, американцы использовали богхед для производства авиационного топлива для обеспечения перелетов самолетов «Дуглас»).
Оленекский богхед-уголь, образовавшийся в результате разложения сапропеля, почти полностью состоит из полинафтеновой фазы и дает 80 % нефти. В 2006 году компания «Нижнеленское» использовала богхед на установке производства ЦНИДИ – данное топливо показало отличные результаты газификации. Характеристики угля для оптимальной газификации представлены в табл. 1.
Способы сжигания твердого топлива
При газификации топливо подается на наклонную решетку, в так называемую первичную камеру сгорания, где оно нагревается до необходимой для протекания процесса температуры. Перегретый и смешанный со вторичным воздухом газ сгорает во вторичной камере сгорания практически без остатка.
К настоящему времени в мире разработаны и применяются несколько технологий газификации. Все процессы осуществляются при атмосферном или повышенном давлении на парокислородном дутье, использовании твердых топлив определенной структуры и различной степени крупности. Это угольные брикеты, древесные пеллеты, щепа, мелкозернистые угли, древесная стружка.
Технологии газификации отличаются способами подготовки и подачи топлива, видом газифицирующего агента (кислород или воздух), структурой и взаимодействием потоков газифицирующих агентов и топлива, способом очистки получаемого горючего газа от примесей. Сначала каждый технологический процесс разрабатывался под конкретный вид топлива. В настоящее время исходное топливо газифицируется разными способами: пылевидное и в виде водоугольной суспензии – в потоке газифицирующих агентов, мелкодисперсное – в псевдосжиженном или циркулирующем слоях, кусковое – в плотном движущемся слое.
Парокислородная газификация пылевидного топлива отличается высокой интенсивностью, в результате получается среднекалорийный продукт – газ с теплотворной способностью 8…16 МДж/кг. Перед подачей в камеру сгорания газовой турбины такой газ практически во всех энергетических схемах разбавляется азотом (является побочным продуктом в установках разделения воздуха) для снижения теплотворной способности и, соответственно, снижения эмиссии высокотемпературных оксидов азота.
При паровоздушной газификации газ является относительно низкокалорийным, с теплотворной способностью 4…7 МДж/кг. Тем не менее, он успешно сжигается в камере сгорания газотурбинного двигателя и обеспечивает требуемый для ее работы уровень температуры продуктов сгорания. Паровоздушная газификация, как правило, сопровождается сухим золоудалением и позволяет перерабатывать низкосортные виды углей.
Главной проблемой очистки получаемого газа является удаление серосодержащих компонентов: H2S, COS и CS2 (в основном, H2S). В развитых технологиях газификации широко применяются адсорбционные и хемосорбционные методы очистки, основанные на использовании жидких сорбентов – различных растворителей и их водных растворов (метанола, диметилэфир полиэтиленгликоля, этаноламинов, метидиэтаноламина и т.д.).
Глубокая очистка газа, тщательная организация процесса его сжигания и применение интегрированных циклов (IGCC) позволяют не только превзойти уровень энергетической и экологической эффективности современных электростанций прямого сжигания пылевого угля, но и сравниться с электростанциями на природном газе. Усредненный химический состав синтез-газа, получаемого в результате газификации угля, представлен в табл. 2.
Технологии газификации угля
В настоящее время существует несколько основных технологий газификации:
• в плотном движущемся слое – угли определенного размера для каждой установки;
• в циркулирующем слое – мелкозернистые угли с размером частиц 2…10 мм;
• в прямоточном режиме – сжигание пылевидного топлива с помощью специальных горелок для сжигания угольной пыли, образующейся в процессе производства или в результате измельчения в пыль: частицы угольной пыли менее 0,1 мм;
• в потоке газифицирующих агентов – угольная пыль менее 90 мкм в виде водоугольной суспензии.
В плотном потоке, который движется в зависимости от направления образующегося синтезгаза, применяют два способа газификации – прямой и обратный.
В обратном процессе кислород подается через специальные воздушные фурмы, расположенные в зоне горения. Отбор генераторного газа идет снизу через регенерирующий слой и выводится через колосниковую решетку, предварительно проходя зону разложения смол, где они разлагаются на горючие газовые составляющие. А поскольку генераторный газ не проходит через слой органики, то он не уносит с собой дополнительно твердые механические частицы. Полученный генераторный газ при обратном процессе газификации намного чище получаемого при прямом процессе, и он может применяться в качестве топлива в газопоршневых электростанциях.
При прямом способе газификации кислород подается снизу через отверстия колосниковой решетки. Получаемый генераторный газ забирается сверху, вынужденно проходя через весь слой газифицируемой органики и унося с собой большое количество твердых механических частиц и пирогенетических смол, образующихся при термическом разложении органики. Такой газ по своей загрязненности и невозможности очистки до требований, предъявляемых к топливу для двигателей внутреннего сгорания, не может применяться в газопоршневых электростанциях. Он может использоваться только в пароводогрейных котлах.
Проект газификации угля в Якутии
Для применения в России полезен опыт Китая, где активно развивается газификация угля. На рис. представлена двухстадийная газогенераторная установка, выпускаемая в Китае.
Особенности конструкции установки:
• Механизм подачи угля: установлен надежный датчик уровня угля, связанный с механизмом подачи, что гарантирует автоматическую подачу в угольный газогенератор, который постоянно находится в состоянии полной загрузки рабочего слоя.
• Питательный механизм угля характеризуется простотой действия, несложным обслуживанием и хорошей герметичностью.
• Внутренняя секция пиролиза, обеспечивающая получение пиролизного газа. Эта конфигурация разработана после строгого расчета теплопередачи и теплообмена, с тем чтобы высушенный уголь полностью коксовался для получения более калорийного газа.
• Газификационная секция: пар используется для получения реакций восстановления и формирования генераторного газа.
• Механизм золоудаления: влажное удаление золы с обеих сторон колесом трещотки со стопором с гидравлическим двигателем. Специальная пластина типа плуга служит для удаления золы, характеризуется устойчивым движением и равномерным вылавливанием зольного остатка.
ОАО «Сахаэнерго» совместно с компанией Flex Technologie разработали проект электростанции мощностью 5 МВт для п. Сангар. В мини-ТЭС будет применяться технология газификации угля с использованием генераторного газа в газопоршневых установках. Характеристики газогенераторной установки CG-32 представлены в табл. 3. Станция разместится в двух зданиях и будет включать:
• угольный склад для хранения оперативного запаса и подачи его в газогенераторы;
• зону газификации для получения из угля чистого генераторного газа, где будут смонтированы три газогенераторные установки (две работают, одна в резерве).
• зону электрогенерации для получения электрической энергии. Она включает десять электроагрегатов (восемь работают, два в резерве) на базе газопоршневого двигателя WJ8300 электрической мощностью 500 кВт.
• зону теплогенерации для получения тепловой энергии в виде горячей воды 90 °С, получаемой путем утилизации тепла охлаждения и выхлопных газов двигателей. Для этого установят 10 пластинчатых теплообменников, 4 водогрейных котла-утилизатора, резервуары-аккумуляторы прямой и обратной воды, трубопроводы, насосы и др.
Схема работы газогенераторной установки
В данной установке забор газа происходит в двух местах, поэтому она называется двухстадийной. Применяется прямой способ газификации: пар и воздух подается снизу, газ отбирается в зоне пиролиза и в зоне восстановления. Температура в нижнем отборе газа составляет 450…550 °С, в верхнем – 90…150 °С, поэтому нижняя часть отбора больше охлаждается.
В установке применяется система автоматического управления с центральным процессором Siemens. Она позволяет отслеживать все важные параметры системы, включать/выключать дискретное оборудование, а также обеспечивать производительность газогенератора в соответствии с выходной нагрузкой электрогенераторов в автоматическом режиме.
Визуальный контроль параметров процесса газификации осуществляется на тактильном дисплее Siemens. При возникновении предаварийных ситуаций, таких как повышение температуры газогенератора или увеличение перепадов давления в газогенераторе и очистительной установке, система управления Siemens выдает оперативные сообщения и выполняет автоматические действия.
Зона электрогенерации
Угольный газ из газогенераторных установок CG-32 после соответствующей подготовки используется в восьми (10) параллельных электрогенераторных установках. Они созданы на основе газопоршневого двигателя WJ8300 электрической мощностью 500 кВт, работающего на 100 %-м угольном газе. Две установки являются резервными (на случай ремонта или поломки других установок). Технические характеристики электрогенераторной установки представлены в табл. 4.
Разработку детального технико-коммерческого предложения выполнил производственный центр ОАО «Сахаэнерго» совместно с компанией «Энергетические схемы и технологии». Сметная стоимость проекта составляет 250 млн рублей.
В 2013 году планируется разработать бизнесплан строительства и рабочий проект газогенераторной мини-ТЭС электрической мощностью 5 МВт. Реализация проекта позволит в дальнейшем создавать электростанции на генераторном газе в местах залегания углей.
Таким образом, применение местных углей вместо завозимого дизельного топлива позволит ежегодно экономить в Якутии более миллиарда рублей. Кроме того, улучшится и экологическая обстановка в регионе. 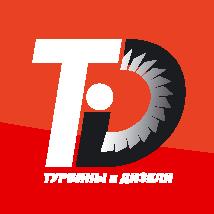