В. Е. Спицын, к.т.н. – ГП НПКГ «Зоря»-«Машпроект»
А. Л. Боцула, С. Н. Мовчан, В. Н. Чобенко, Д. Н. Соломонюк – ЦНИОКР «Машпроект»
ГП НПКГ «Зоря»-«Машпроект» работает над созданием регенеративного двигателя мощностью 16 МВт для привода нагнетателя природного газа с 2008 года. Выполненные проработки подтвердили возможность создания регенеративной ГТУ номинальной мощностью 16 МВт с КПД не менее 40 %.
В настоящее время газотурбинные установки являются основным типом привода компрессоров природного газа на компрессорных станциях. В газотранспортной системе Украины суммарная мощность ГТУ составляет более 80 % общей мощности всех ГПА. На сегодня большая часть этих агрегатов выработала свой ресурс и физически и морально устарела. Средний КПД двигателей, установленных на большинстве газокомпрессорных станций Украины и России, не превышает 26 %. В этих условиях становится очевидной необходимость создания и применения для транспортировки газа современных эффективных приводов с более высоким значением КПД.
Основными требованиями, предъявляемыми к перспективным газотурбинным установкам для привода компрессора природного газа, являются [1, 2, 3]:
• высокая экономичность (КПД 35-40 % в зависимости от мощности ГТД);
• низкая эмиссия оксидов азота и оксида углерода (менее 50 мг/м3);
• большой общий ресурс (120-150 тыс. ч) с ресурсом до капитального ремонта 40-50 тыс. ч;
• наработка на отказ более 10 тыс. ч;
• простота и удобство обслуживания, возможность ремонта в условиях компрессорной станции;
• модульность конструкции;
• невысокая стоимость.
Результаты анализа предъявляемых к ГТД требований и современного уровня развития отечественных технологий показывают, что в настоящее время для создания высокоэффективного и надежного газотурбинного привода целесообразно использовать схему с регенерацией тепла уходящих газов. Такая схема позволяет при умеренных значениях степени повышения давления в компрессоре и температуры газа на входе в турбину, в значительной степени определяющих надежность установки, получить высокие значения экономичности. Перспективность данного направления подтверждается интересом и практическими результатами работы ведущих мировых производителей газотурбинных двигателей.
В качестве примера таких установок, реализованных в последнее время, можно привести Мегсuгу 50 (Solar Turbines Incorporated) и WR21 (Westinghouse-Rolls-Royce). На российском рынке предлагаются проекты создания регенеративных установок так называемого сухого «бинарного» цикла» – ГТУ-27ПС (производства ОАО «Авиадвигатель») и «Надежда» (Невский завод).
Научно-исследовательские работы по созданию регенеративного ГТД ведутся в ЦНИОКР «Машпроект» с 1990 года. Основную сложность представляет создание высокоэффективного и надежного регенератора, имеющего приемлемые массогабаритные и стоимостные показатели. Конструкции пластинчатых и трубчатых регенераторов проекта ГП НПКГ «Зоря»-«Машпроект» для судовых и стационарных ГТУ, а также их основные параметры приведены в [4]. Там же выполнен анализ целесообразности применения различных типов и компоновок поверхности теплообмена регенераторов.
С 2008 года ГП НПКГ «Зоря»-«Машпроект» работает над созданием регенеративного ГТД мощностью 16 МВт для привода нагнетателя природного газа. Выполненные проработки подтвердили возможность создания регенеративной ГТУ номинальной мощностью 16 МВт с КПД не менее 40 % [5].
Исходя из требований надежности, низкой стоимости и ресурса, предъявляемых к газотурбинным приводам компрессоров природного газа, значение температуры газа на входе в турбину принято ~950 °С [5], что позволяло обойтись без охлаждения рабочих и сопловых лопаток первой ступени турбины. При этом для повышения надежности и удешевления регенератора температура выхлопных газов на выходе из ГТД ограничивалась 600 °С, что позволяло обеспечить температуру теплообменных поверхностей на уровне 560…580 °С и применить в регенераторе низколегированные и достаточно дешевые стали.
Более детальная проработка узлов ГТУ [6] показала, что при предварительно принятых параметрах цикла (температура газа на входе в турбину 950 °С и степень повышения полного давления в компрессоре – 5) и уточненных значениях потерь в проточной части ГТД и регенераторе КПД установки составит 39 %, а температура газа на входе в регенератор превысит 600 °С.
Оценка теплонапряженного состояния рабочей лопатки турбины компрессора показала, что для обеспечения требуемого ресурса необходимо введение охлаждения пера лопатки. Охлаждение рабочих лопаток турбины компрессора приводит к некоторому снижению ее КПД, но в то же время позволяет рассматривать возможность его увеличения за счет повышения температуры газа на входе в турбину. После анализа параметров цикла [6] установлено, что для обеспечения расчетного значения КПД установки более 40 % необходимо увеличить температуру газа на входе в турбину примерно до 980 °С и степень повышения полного давления воздуха в компрессоре до 5,75, что позволит обеспечить температуру газа на входе в регенератор менее 600 °С.
При принятых параметрах цикла основные расчетные показатели ГТУ в условиях компрессорной станции при стандартных атмосферных условиях составят:
• мощность на выходном валу ГТД – 16 МВт;
• КПД двигателя – 40,3 %
• расход воздуха на входе в ГТД – 74,9 кг/с;
• степень повышения давления в компрессоре – 5,75;
• степень регенерации – 0,85;
• температура газа на входе в турбину – 980 °С;
• температура газа на выходе из турбины – 590°С;
• температура газа на выходе из регенератора – 306 °С.
Предполагается создание ГТУ с номинальной частотой вращения силовой турбины 5200 об/мин. Такие установки могут применяться в газоперекачивающих агрегатах с современными и перспективными компрессорами природного газа, оснащенными высокоэффективными сменными проточными частями (СПЧ). По данным СНПО им. М.В. Фрунзе, при использовании компрессора с номинальной частотой вращения 6500 об/мин возможно создание унифицированного компрессора для агрегатов линейных и дожимных компрессорных станций с КПД более высоким, чем у существующих серийных образцов. Однако повышение частоты вращения ротора силовой турбины приводит к уменьшению КПД двигателя вследствие увеличения потерь с выходной скоростью. При этом появляются существенные проблемы с обеспечением прочности деталей силовой турбины и необходимых запасов по критическим частотам системы роторов «СТ ГТД, газовый компрессор, трансмиссия».
По результатам предварительных расчетных проработок приняты следующие конструктивные решения:
• компрессор – 11-ступенчатый, создается на базе компрессора ГТД ДМ80Л путем добавления двух ступеней на выходе для обеспечения требуемой степени повышения полного давления воздуха. Передняя опора компрессора – комбинированная, с двухсторонним упорным подшипником скольжения и опорным роликовым подшипником. Конструкция передней опоры компрессора должна обеспечивать возможность осевого отбора мощности на привод редуктора вспомогательных механизмов (в т.ч. электрогенератора собственных нужд). Задняя опора – роликоподшипник, установленный на упругодемпферную втулку;
• камера сгорания – кольцевая, двухзонная, с меридиональным разъемом жаровой трубы по передней и задней стенкам для обеспечения возможности ее замены в эксплуатации. Конструкция камеры сгорания обеспечивает отвод воздуха из-за компрессора к регенератору без контакта с поверхностями жаровой трубы и смесителя;
• турбина компрессора – одноступенчатая, с конвективным охлаждением сопловых и рабочих лопаток;
• силовая турбина – одноступенчатая, консольная. Передняя опора – роликоподшипник, задняя – комбинированная (подшипник скольжения).
Продольный разрез газотурбинного двигателя приведен на рис. 1.
Одной из задач, которую необходимо было решить при создании данной установки, являлась разработка конструкции регенератора. Она должна иметь минимальные массогабаритные показатели теплообменника (с обеспечением требуемых значений передаваемого тепла и потерь давления теплоносителей), обеспечивать надежность и долговечность, а также ремонтопригодность регенератора.
В результате проектно-конструкторских работ была создана конструкция трубчатого двухсекционного регенератора (конструкция одной секции представлена на рис. 2). Поверхность теплообмена 1 набрана из плоских параллельных змеевиков, расположенных в прямоугольном коробе 3, который является естественной частью газохода ГТД. Схема движения теплоносителей в регенераторе – многократный перекрестный ток с общим противотоком. Уходящие газы обтекают трубки снаружи, воздух течет внутри трубок и подводится (отводится) по круглым коллекторам. Воздух совершает шесть ходов, уходящие газы – один ход. Между ходами по периметру газохода установлены вытеснители 9.
Змеевики теплообменника набираются из гладких труб диаметром 22 мм и толщиной стенки 1 мм и при сборке образуют плотную поверхность теплообмена, трубки в которой расположены в шахматном порядке (рис. 3). Компоновка пакета такова, что осевые линии теплообменных труб в каждом ходе теплообменника и между ходами расположены параллельно, и, таким образом, поверхности трубок не соприкасаются (несмотря на то что плоскости змеевиков частично перекрываются). Переход воздуха из одного хода в другой осуществляется по гнутым калачам 2, расположенным в шахматном порядке. Шаг калачей вдоль оси коллектора равен шагу змеевиков, а шаг поперек оси коллектора (в отличие от аналогичных конструкций) уменьшен до величины, обеспечивающей минимальный зазор между трубками.
Воздух подводится и отводится из змеевиков пакета по цилиндрическим коллекторам постоянного сечения (7 и 8). В отличие от аналогичных конструкций коллекторы собираются из двух полуцилиндров разной толщины при помощи плоских фланцев, приваренных вдоль их оси. С торцов к полуцилиндрам приварены половинки кольцевых фланцев, которые при сборке коллекторов образуют фланцы для присоединения трубопроводов отвода и подвода воздуха. С противоположной стороны от трубопроводов подвода-отвода коллекторы закрываются заглушками.
Особенностью данной конструкции является также то, что трубки соединяются с коллекторами при помощи гнутых отводов 6. Продольный шаг по ходу газа между отводами в месте их входа в коллектор увеличен вдвое по отношению к шагу трубок в пучке. Концы отводов выступают вглубь коллектора.
Для поддержания змеевиков и обеспечения требуемых шагов между трубками применяются плоские вертикальные проставки (см. рис. 2 и 3), которые верхними концами приварены к силовым балкам корпуса 5, расположенным над теплообменным пакетом. Концы балок проходят через стенку корпуса и крепятся к его силовому набору. Торцы балок оставлены открытыми. Нижние концы проставок зажимаются между уголками, приваренными к корпусу.
Результаты расчетных и конструкторских работ подтверждают возможность создания ГПА регенеративного цикла номинальной мощностью 16 МВт с КПД более 40 %. Предварительная компоновка такого агрегата показана на рис. 4. Конструктивные решения, принимаемые при создании газотурбинной установки регенеративного цикла, предусматривают максимальное использование отработанных в производстве и проверенных в эксплуатации элементов и узлов двигателя. Это позволяет сократить сроки создания ГТУ и обеспечить ее высокую надежность и эффективность.
Теплогидравлические расчеты, проведенные для спроектированного регенератора, показали, что для ГТУ мощностью 16 МВт степень регенерации будет не ниже 0,85, а суммарное гидравлическое сопротивление его трактов не превысит 4 %, что обеспечивает КПД двигателя на уровне 40,3 %.
В настоящее время для экспериментальных исследований разработанной конструкции создана модель, которая будет проходить испытания в одной из лабораторий ЦНИОКР «Машпроект».
С целью дальнейшего совершенствования конструкции регенератора и уменьшения его массогабаритных показателей ГП НПКГ «Зоря»-«Машпроект» и ИТТФ НАН Украины ведут совместные исследовательские работы по изучению возможности применения в регенераторе трубчатых поверхностей с интенсификаторами теплоотдачи (лунки, выступы и др.).
Использованная литература:
1. Щуровский В.А. Состояние и перспективы применения газотурбинных и компрессорных технологий//Газовая промышленность. 2003. № 2. С. 41-44.
2. Щуровский В.А. Основные направления развития газоперекачивающей техники// Газотурбинные технологии. 2007. № 6. С. 38-39.
3. Типовые технические требования к газотурбинным ГПА и их системам. СТО Газпром 2-3.5.138-2007, 55 с.
4. Мовчан С.Н., Бочкарев Ю.В., Соломонюк Д.Н. Этапы развития стационарных и судовых газотурбинных установок с регенерацией теплоты//Газотурбинные технологии. 2008. №8. С. 8-11.
5. В.Е. Спицын, А.Л. Боцула, Д.Н. Соломонюк, В.Н. Чобенко. Высокоэффективная газотурбинная установка для ГПА//Вісник Національного технічного університету «Харківський політехнічний інститут». 2008. № 34. С. 3-6.
6. Романов В.В., Спицын В.Е., Боцула А.Л., Мовчан С.Н., Чобенко В.Н. Особенности создания газотурбинной установки регенеративного цикла для ГПА//ВосточноЕвропейский журнал передовых технологий. 2009. №4. С. 16-19. 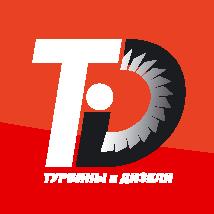