А. Н. Безъязычный, Д. И. Колосов – ОАО «ОДК–Газовые турбины»
На предприятии «ОДК–Газовые турбины» (ОДК–ГТ) в г. Рыбинске введен в промышленную эксплуатацию универсальный испытательный стенд – он представляет собой большой испытательный цех. Общая площадь испытательного комплекса составляет 6500 м2. Это первый в России стенд для полноразмерных заводских испытаний энергетических и газоперекачивающих агрегатов широкого диапазона мощности.
Наличие собственной испытательной базы полностью соответствует требованию стратегических партнеров компании «ОДК–Газовые турбины» о проведении испытаний оборудования на базе предприятия. В торжественном мероприятии по вводу испытательного комплекса приняли участие губернатор Ярославской обл. С.Н. Ястребов, зам. генерального директора ОАО «ОДК» С.П. Павлинич, зам. генерального директора ООО «Газпром комплектация» Б.Я. Имас, начальник управления энергетики департамента по транспортировке, подземному хранению и использованию газа ОАО «Газпром» В.В. Гоголюк, представители компаний «ВНИИГАЗ», «Роснефть», «ВТБ» и др.
Испытательный стенд построен в рамках государственного контракта «Создание основ серийного производства типового ряда энергоустановок мощностью до 50 МВт для оснащения объектов электротеплоснабжения небольших и средних городов и городских районов». Контракт предусматривает создание в Рыбинске крупной промышленной базы для производства энергетического оборудования.
Договор был заключен между ОАО «ОДК– Газовые турбины» и Министерством промышленности и торговли РФ в мае 2012 года. Финансовую поддержку в строительстве стенда оказал банк «ВТБ». Кроме того, компания «ОДК–ГТ» выполнит НИОКР по разработке энергетических установок модульного типа мощностью до 50 МВт.
Первым агрегатом, прошедшим испытания на стенде компании в июле 2014 г., стал ГТА-10ГТ мощностью 10 МВт. Сегодня на стенде проходит испытания ГТА-16 электрической мощностью 16 МВт, изготовленный по заказу ООО «Газпромнефть Новый порт». Это первый энергетический агрегат разработки «ОДК–ГТ» такой мощности.
Предприятие изготовит и поставит для энергоснабжения объектов нефтедобычи Новопортовского нефтегазоконденсатного месторождения шесть энергоустановок. Энергоблоки созданы на базе двигателей ГТУ-16П производства Пермского моторного завода (разработка ОАО «Авиадвигатель»).
На стенде проводятся испытания газопоршневых энергоустановок в диапазоне мощности 0,5…4,0 МВт, газотурбинных энергоблоков собственного производства предприятия в диапазоне мощности до 25 МВт – ГТЭС-2,5; ГТА-6/8РМ; ГТА-10ГТ; ГТА-14 на базе Titan-130; ГТА-16; ГТА-25. Газоперекачивающие агрегаты, выпуск которых освоен и планируется на предприятии – ГПА-4РМ; ГПА6,3/8РМ; ГПА-16; ГПА-25, начнут испытываться с 2015 года.
В сегодняшних условиях наличие собственного испытательного стенда дает компании серьезное конкурентное преимущество, позволяя участвовать в конкурсах, где одним из основных требований является проведение испытаний агрегатов в заводских условиях. Кроме того, испытания на базе завода-изготовителя значительно сокращают сроки монтажа и пусконаладки оборудования на объектах заказчиков, обеспечивают надежную эксплуатацию продукции.
С вводом испытательного комплекса значительно сократится время перехода от опытного образца к серийной продукции. Будет обеспечена возможность проводить комплексные испытания энергетических и газоперекачивающих агрегатов широкого мощностного ряда с выходом на номинальный режим. А это, в свою очередь, позволяет контролировать параметры, которые формируются на стадии проектирования и определяются техническими условиями. В этом случае предприятие может гарантировать, что заказчик получит надежный, прошедший комплексные испытания агрегат, технико-экономические характеристики которого полностью доказаны.
Учитывая географию поставок продукции «ОДК–ГТ» (в т.ч. Крайний Север, Сибирь, Дальний Восток и т.д.), очевидно, что проведение корректировок, необходимость в которых появляется в процессе пусконаладки на местах, очень дорогостоящая процедура. В связи с этим руководство компании пришло к решению о строительстве стенда, получив при этом поддержку ОДК.
В ходе создания стенда были приняты основные технические решения, позволяющие проводить испытания энергетических и газоперекачивающих агрегатов блочного и цехового исполнения. В 2013 г. была разработана проектная документация стенда и пройдена государственная экспертиза, в том же году предприятие приступило к строительству испытательного комплекса. Параллельно с монтажом технологических сетей проводился монтаж энергетического агрегата ГТА-10ГТ и электромонтаж межблочных связей.
При создании такого сложного объекта необходимо было выполнить большой объем проектных и строительно-монтажных работ. Сюда входило и строительство основного здания стенда, и вспомогательных зданий и сооружений – высоковольтной эстакады, помещений для комплексных распределительных устройств, ДКС, трансформаторной подстанции, станции пожаротушения. Было изготовлено большое количество нестандартного технологического оборудования – КВОУ для подготовки подвода циклового воздуха и устройство для отвода отработавших газов.
Для испытания оборудования в трех функциональных отсеках созданы восемь унифицированных боксов – для ГПЭС, ГТЭС и ГПА различной мощности. Каждый бокс оснащен системой подвода циклового воздуха и отвода выхлопных газов. К нему подходят газовая и электрические магистрали, информационные кабели для проведения всего комплекса испытаний.
Испытательный стенд оснащен автоматизированной системой управления технологическими процессами. АСУ ТП обеспечивает в oнлайн-режиме сбор и систематизирование показателей систем обеспечения стенда (дожимная компрессорная станция, система пожаротушения, системы обеспечения электроэнергией и сжатым воздухом). Дополнительно САУ испытываемого агрегата интегрируется с АСУ ТП стенда. Данные выводятся дистанционно на пульт оператора для контроля и оперативного вмешательства в процесс управления всеми без исключения системами стенда и испытываемых агрегатов.
Для сжатия и подачи топливного газа в процессе испытаний всех типов ГТА и ГПА применяется дожимная компрессорная установка EGSI-S-140/1400WA производительностью до 16 тыс. м3/ч. Давление на станции повышается с 1,2 до 5,0 МПа. Поставку и шефмонтаж компрессорной установки осуществила компания «Энергаз».
Современные модульные электронагрузочные устройства производства Crestchic Loadbanks общей мощностью 25 МВт позволяют проводить испытания под нагрузкой для всей номенклатуры газопоршневых и газотурбинных энергетических агрегатов, выпускаемых предприятием. Шаг увеличения нагрузки 1 кВт позволяет дать высокоточную оценку параметров мощности агрегата.
Для транспортировки модулей агрегатов используются две самоходные многоколесные тележки грузоподъемностью по 65 тонн производства компании Wheelift. Тележки с дистанционным управлением обеспечивают очень удобное передвижение энергоблоков и их установку на месте испытания в условиях ограниченного пространства. Такой способ перемещения является прекрасной альтернативой козловому крану большой грузоподъемности.
Система крепления агрегатов на стенде во время испытаний и система опор трубопроводов создана совместно с компанией Halfen. Использование быстросъемных болтов и шинорельсов обеспечивает точность стыковки узлов агрегата между собой, быстроту монтажа и демонтажа, надежность крепления к основанию. Установка агрегата на стенд, подключение всех систем и подготовка к испытаниям у серийных образцов будет занимать несколько рабочих дней (без учета ПНР). По окончании монтажа и пусконаладочных работ систем агрегата начинается непосредственный процесс испытания. Он включает технологическую прокрутку двигателя, выход на холостой ход, выход под нагрузку (ступенчато для каждого агрегата, оговорено программой испытания), испытания на различных мощностных режимах и временных интервалах, снятие нагрузки (также ступенчато).
Комплексные заводские испытания позволяют:
• проводить проверку качества изготовления и сборки агрегатов, проверку работоспособности систем агрегата и его составных частей;
• имитировать синхронизацию энергоблоков с сетью, сброс и наброс нагрузки в максимальных пределах, нагрузку агрегатов до номинальной мощности, проверить вибросостояние на опорах ГТД и турбогенератора;
• выполнить несколько запусков газоперекачивающего агрегата, проверить стабильность запуска ГПА, выход на режим холостого хода без заполнения контура нагнетателя, работу агрегата на холостом ходу.
С вводом универсального испытательного стенда компания «ОДК–Газовые турбины» получила возможность контролировать все заложенные проектом технические параметры оборудования, выявить и устранить дефекты, оперативно провести НИОКР по доводке и совершенствованию отдельных узлов и агрегата в целом. Благодаря комплексным испытаниям сроки монтажа и пусконаладки блочных энергоустановок сократятся более чем в четыре раза.
Таким образом, на предприятии создан современный испытательный комплекс, на котором можно одновременно проводить различные испытания нескольких агрегатов. Контрольные заводские, приемосдаточные и сертификационные испытания газотурбинных и газопоршневых агрегатов, а также компрессорных установок будут проводиться не только в широком диапазоне мощности, но и с применением самой передовой техники и технических решений, имеющихся на сегодня в мире. 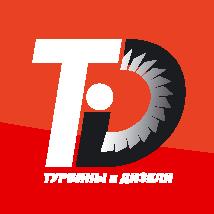