Е. М. Хвоенков, Е. М. Хейфец – ООО «ТМ МАШ»
Масштабная реконструкция тепломеханической части энергоцентра завода «ГЗОЦМ» в г. Гай Оренбургской области позволила вывести на проектную мощность систему теплоснабжения предприятия. В рамках проекта выполнена комплексная замена тепломеханической системы мини-ТЭС, включающая как изготовление нового оборудования, так и разработку тепловой схемы и обновленного алгоритма работы.
С мая по октябрь 2014 года специалисты компании «ТМ МАШ» выполнили работы по комплексной модернизации существующей тепломеханической системы завода «ГЗОЦМ». Энергоцентр был создан на базе пяти газопоршневых установок Cummins С1540 GQNA (электрическая мощность 1540 кВт) с двухконтурной системой утилизации тепла (СУТ), поставленной в комплекте с ГПУ в 2012 году. СУТ создана на базе пластинчатых утилизаторов тепла антифриза и водотрубных утилизаторов тепла дымовых газов.
В ходе эксплуатации станции возникла проблема: через несколько месяцев после начала работ поставленные в комплекте с ГПУ котлы-утилизаторы дымовых газов полностью вышли из строя. Выяснилось, что причиной поломки стала некорректная работа системы водоподготовки, в результате чего теплообменники покрылись минеральными отложениями (накипью). Конструкция водотрубных утилизационных теплообменников не позволила произвести их очистку и ремонт оборудования.
Предприятию «ТМ МАШ» было предложено изготовить новые модули утилизации тепла дымовых газов. В ходе первичной проработки конструкции СУТ специалисты компании предложили изменить проект, чтобы избежать появления минеральных отложений на теплообменниках в будущем. Основная задача изменений состояла в том, чтобы разделить контур СУТ и контур нагреваемой сетевой воды. В результате был согласован и выполнен определенный объем работ.
Проектные работы
Гидравлическое разделение контуров. Работы предусматривали создание цикличного контура СУТ и связанного с ним через разделительный теплообменник контура сетевой воды. Таким образом, попадание неподготовленной воды в котлы-утилизаторы стало невозможным. Общая насосная группа осталась на стороне сетевой воды. В целях экономии было решено не закупать новое оборудование, а использовать ранее установленные сетевые насосы.
Изменение тепловой схемы. В созданном контуре СУТ на подводе к каждой машине был установлен собственный насос. Создание такой насосной группы позволяет добиться эффективного и равномерного расхода нагреваемого теплоносителя по всем тепловым модулям. Равномерность потоков положительно влияет на эффективность системы, а также на срок ее службы. В контур утилизации тепла добавлена система подпитки.
Замена утилизаторов тепла. Объем проектирования включал разработку последовательности демонтажа установленных котлов-утилизаторов, порядок установки ТММТМВГ.1000, проектирование трасс подвода и отвода нагреваемой среды, конструкции байпаса и прочих элементов обвязки.
Изготовление оборудования
Пять тепловых модулей утилизации тепла дымовых газов ТММ-ТМВГ.1000 с жаротрубными котлами-утилизаторами.
Модули включали в себя котлы-утилизаторы тепловой мощностью 1025 кВт и переключатели потока на линии выхлопных газов. Оборудование смонтировано на единой раме. Байпасная линия изготовлена силами заказчика, с частичным использованием узлов установленного ранее оборудования. Документацию по замене блоков утилизации тепла разработали специалисты «ТМ МАШ».
Жаротрубные теплообменники компактно вписались в существующее здание. Изготовление дополнительных опорных конструкций и значительное изменение линий подвода/ отвода воды не потребовалось.
Разделительный теплообменник ТММРТА.8250 мощностью 8250 кВт. Установка данного теплообменника сделала весь контур утилизации тепла замкнутым и не зависящим от качества сетевой воды.
Изготовленный разделительный теплообменник – кожухотрубного типа. Рабочее тело (подготовленная вода) контура СУТ находится в межтрубном пространстве, сетевая вода (нагреваемая среда) проходит через трубки. Конструкция ТММ-РТА имеет откидную камеру на петлях и люки для прочистки. Это позволяет очистить трубное пространство в сжатые сроки и без специального инструмента.
Объединенный шкаф управления ТМВГ для размещения в операторской. Шкаф управления получает данные о температуре среды на выходе из каждого котла-утилизатора и управляет переключателем потока выхлопных газов. По требованию заказчика пять шкафов управления объединены в одном корпусе – это позволило сэкономить место в операторской, а также повысить наглядность отображения информации.
В результате выполнения данных работ были достигнуты следующие результаты:
• система утилизации тепла на станции заработала в полную силу. После запуска оборудования на полную мощность тепловая мощность мини-ТЭС составила 8250 кВт;
• замкнутый контур СУТ исключает зависимость от качества сетевой воды. Контур заправлен подготовленной по РД 34.37.504-83 водой. Система подпитки обеспечивает стабильность работы;
• низкие затраты при замене оборудования и монтаже элементов измененной СУТ достигнуты за счет максимального использования уже установленного оборудования и трубопроводов.
Реконструкция энергоцентра Гайского завода по обработке цветных металлов завершилась в декабре 2014 года. В результате модернизации экономия газа, сжигаемого в котельной, составила в месяц до 582000 м3 на сумму около 3 млн рублей (при круглосуточной загрузке пяти ГПУ). 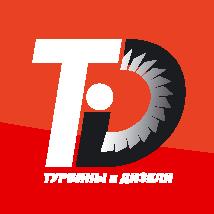