В.С. Беляков, С.С. Чернышев, В. О. Рыхтер – ЗАО «Автономный энергосервис»
Компания Guascor Power работает на рынке с 1964 года. Сегодня это один из ведущих европейских производителей двигателей для морских судов и промышленных электростанций различного назначения. Оборудование Guascor, работающее на дизельном топливе, природном и попутном газе, биогазе, за многие годы доказало свое неизменное качество и высокую надежность.
Компания на протяжении всей своей деятельности особое внимание уделяет совершенствованию продукции и разработке новых решений для различных рынков. Так, первые электростанции серии FG отличаются от пятого поколения (серия HGM) примерно так же, как автомобили начала 1990-х годов отличаются от современных машин. Более того, выпускаемые сегодня электростанции Guascor малой мощности FG180 и FG240 аналогично отличаются от своих прототипов. Все это достигнуто за счет использования новейших технологий и совершенствования применяемых технологических решений.
Эволюция производства Guascor затронула все этапы создания оборудования – начиная от процесса проектирования и производства и заканчивая эксплуатацией. В частности, с 1989 г. (начало разработки первых станций серии FG) ресурс до капитального ремонта вырос уже более чем вдвое (с 30000 ч до 64000 ч) и далее будет увеличиваться.
Такое совершенствование обусловлено, в первую очередь, развитием материалов. Благодаря созданию новых сплавов и изолирующих материалов, оборудование способно выдерживать большие нагрузки в течение длительного времени. Косвенно это влияет и на другие области: используются качественно новые технологии, системы управления выполняют более сложные задачи и т.д.
Следующим фактором, повышающим надежность и работоспособность двигателей, является использование принципиально новых технологий, которые ранее либо не применялись в отрасли, либо были разработаны за время эксплуатации оборудования (например, в области контроля детонации). В связи с этим, понимая чрезвычайную важность регулярного внедрения технических новинок, в компании Guascor был создан собственный исследовательский центр, работа которого направлена на разработку и тестирование технологий для дизельных и газовых двигателей.
Существенным фактором является также опыт наработки и эксплуатации оборудования. Ведь только фактические количественные показатели отражают степень надежности, которая достигается при внедрении технических новинок. Все это делает Guascor одним из лидеров отрасли, так как помимо данных, получаемых от исследовательского центра, компания имеет обширную сеть объектов собственной генерации, где используются свои электростанции. На протяжении длительного времени собственная генерация – одно из направлений бизнеса концерна Guascor. Обширная сеть электростанций для генерации и последующая продажа электроэнергии оптимизирует ее себестоимость.
Эксплуатация собственных объектов генерации позволяет максимально эффективно оптимизировать интервалы проведения ТО и замены компонентов, обеспечить проектировщиков необходимой информацией относительно того, какие узлы следует модернизировать. Иными словами, получить полнейший объем информации для достижения главной цели – снижения расходов на электроэнергию.
Главное в подходе компании Guascor – оптимизация расходов клиента. Электростанции не обязательно будут иметь самый высокий КПД, но они непременно должны быть самыми выгодными в эксплуатации. Суть подхода к разработке, сборке и последующей эксплуатации оборудования проста: станция должна обеспечивать выработку электроэнергии с минимально возможной себестоимостью.
Затраты на выработку электроэнергии складываются из большой совокупности факторов: расход топлива, затраты на запасные части, ТО, на персонал и пр. Особенность заключается в том, что если взять любой отдельный объект, то некоторые составляющие на нем будут одинаковы для любой марки станции: количество персонала, стоимость проектирования (при условии использования одинакового количества электростанций с равной мощностью). Различия будут заключаться в таких показателях, как расход топлива (и его производный показатель – КПД), затраты на запчасти, расходные жидкости и обслуживание. Стоимость самого оборудования также может отличаться. Очень важно понимать, что стоимость оборудования увеличивается с ростом стоимости технологий, которые в нем применяются. Однако это не означает, что если оно дороже на 20 %, то будет на 20 % надежнее или качественнее. Отличия будут, но будут ли они существенными? Применяемые технологии обусловлены конструкционными решениями, а они, в свою очередь, позволяют получить те или иные выходные характеристики.
Как и в любой отрасли, чем лучше итоговые параметры (например, КПД), тем дороже обойдется сборка оборудования. Иными словами, там, где один производитель для получения КПД 39,5 % затратил Х рублей, другой – для получения КПД 40,1 % использовал Х х 1,1 р. При этом разница в 0,6 % КПД обходится заказчику в дополнительные 10 % стоимости оборудования. Стоит ли игра свеч? Если в Европе, где стоимость газа существенно выше, такой подход иногда актуален (обосновать может только экономический расчет на конкретный объект), то в российских условиях эта разница никогда не окупится.
Еще одним фактором, влияющим на стоимость эксплуатации, является стоимость запасных частей и ТО. Удорожание технологий автоматически влечет за собой использование более дорогих компонентов и необходимость в более сложных работах при проведении регулярного обслуживания.
Снизить стоимость эксплуатации можно, если увеличить межсервисные интервалы. Однако расширение интервалов влечет за собой то же, что и использование более дорогостоящих технологий: компоненты двигателя, подлежащие замене (свеча, фильтр или прокладка), должны быть выполнены из более прочного и дорогого материала. Что из этого следует?
Рассмотрим пример. Замена масляного фильтра на одной электростанции производится через 2000 ч, а на другой – через 4000 ч. Соответственно, отработавший меньшее время фильтр будет дешевле. И здесь важно то, что стоимость фильтра, который способен работать большее количество времени, может быть выше не в два, а в два–три раза. Поэтому, с точки зрения эксплуатации, гораздо экономичнее дважды сменить более дешевый фильтр.
Такой подход применим для любого компонента электростанции Guascor. Именно такими интервалами замены и обусловлен итоговый срок до капитального ремонта – он ограничен интервалом замены критичных крупных узлов. Нужно заметить, что срок работы оборудования до капитального ремонта, даже с учетом всего вышеприведенного, в настоящий момент у всех производителей одинаков и составляет 60000…64000 часов (лишь у некоторых 48000 ч).
Следуя своей философии, компания Guascor в первую очередь производит оборудование, оптимальное по соотношению цена/характеристики. В 1996 г., учитывая потребности рынка и новые требования, предъявляемые к оборудованию, компанией был создан новый Центр исследований и развития, который по праву считается одним из лучших в мире. В распоряжении Guascor имеются 22 испытательных стенда (включая гидравлические тормоза, редукторы, генераторы, стенды измерения сопротивления, хроматографические газоанализаторы), а также лаборатория электронного оборудования, цех сборки и испытаний двигателей.
В технологическом центре Guascor применяются самые современные компьютерные CAD-программы и программы расчета нагрузок, основанные на методе конечных элементов, для комплексного проектирования газовых и дизельных двигателей. На сегодня такие методики являются самыми прогрессивными. Испытания и анализ работы двигателей позволили Guascor использовать новейшие технические решения для оптимизации их производительности, прочности и выносливости.
Благодаря исследовательскому центру, испытания оборудования ведутся в реальных условиях, накоплена огромная статистика и опыт эксплуатации. Все вводимые изменения следуют четкой схеме – повышение надежности и эффективности при обязательном снижении издержек заказчика.
Например, свечи – один из важных компонентов системы зажигания. Базовая конструкция свечи зажигания не изменилась с прошлого века. Первые электроды были стальными, а изоляторы изготавливались из фарфора или огнеупорной глины, и разрушались они гораздо быстрее остальных элементов свечи. Теперь окись алюминия смешивают с добавками, прессуют в формах под давлением 30 МПа и спекают при температуре 1500 °С, а после остывания покрывают глазурью для уменьшения вероятности поверхностного разряда.
Электроды (и центральный, и боковой) раньше изготавливались из той же низкоуглеродистой стали, что и корпус. Стойкость к эрозии выдвинула на первый план хромоникелевые сплавы, из которых делают современные электроды. Новые модели укомплектованы платиновыми вставками в виде дисков на боковом или на обоих электродах. Платина намного устойчивей к коррозии и электрохимическому разрушению.
За 150 лет свечи прошли длительный путь развития. Сегодня компания Guascor применяет и обычные свечи, и платиново-иридиевые, имеющие значительный ресурс. Применяется принудительное охлаждение гнезд свечей для увеличения их ресурса.
Также заказчику предлагаются форкамерные свечи зажигания. Принцип их действия основан на использовании сопла Лаваля, в котором газовоздушная смесь получает значительное ускорение. Такие свечи повышают мощность и снижают расход топлива. Форкамерные свечи в газопоршневых агрегатах Guascor позволяют зажигать обедненную смесь в капсульном конце даже при низкой энергии зажигания, а пять отверстий для выхода искры – добиться надежного горения. Пламя поступает в открытую камеру сгорания, которая меньше изнашивается под воздействием температуры, а также более экологична в отношении выбросов.
Технологии в изготовлении изолирующих материалов за последние десятилетия достигли значительного прогресса. Если раньше они создавались на базе резины и природных высокотемпературных материалов, теперь, например, активно применяются прокладки из современных, стойких к воздействию ГСМ и температур материалов. Новые герметики позволяют значительно облегчить ремонт и качество прилегания сопрягаемых поверхностей. Компания Guascor использует разные изолирующие материалы в зависимости от условий эксплуатации: разработаны решения как для рынка РФ, предназначенные для работы оборудования в экстремальных условиях, так и для стран с теплым климатом.
Для газопоршневого двигателя критична высокая средняя температура термодинамического цикла, что требует постоянного контроля температуры цилиндров и обеспечения их защиты. Повышение температуры сгорания топлива может вывести из строя турбонагнетатели, поршни, клапанный механизм, а отклонение температуры цилиндра от средней в меньшую сторону может являться следствием проблем с системой зажигания, критического повреждения или износа цилиндропоршневой группы. С целью повышения антифрикционных характеристик поверхностей и их износостойкости применяются специальная обработка и покрытия, которые в разы повышают ресурс поршней и других трущихся элементов мотора. В исследовательском центре Guascor выполняется подбор специфических материалов для разных условий эксплуатации (температура, давление, воздух для горения) и типов газа (ПНГ, биогаз, шахтный метан и др). Это повышает ресурс оборудования и улучшает экономику проекта.
Использование передовых электронных систем зажигания, в отличие от механических, существенно снижает расход топлива двигателя и износ многих элементов. Адаптивность системы позволяет в автоматическом режиме осуществлять необходимые регулировки в соответствии с заложенными алгоритмами. При этом заказчик может выбрать максимально простые системы регулирования.
Электронные системы управления двигателем позволяют существенно снизить уровень детонации – взрывообразного сгорания топлива, крайне опасного для двигателя, которое может привести к его полному разрушению. Детонация приводит к снижению мощности, выходу из строя клапанного механизма и повреждению деталей цилиндропоршневой группы двигателя. Применяемые блоки автоматики и контроль работы каждого цилиндра за счет индивидуальных датчиков предоставляют широкие возможности по использованию встроенной, свободно программируемой логики, позволяя управлять сложными регулирующими устройствами.
Следствием вышеперечисленного является продление межсервисных интервалов для электростанций Guascor, которые основаны на подходе оптимального регламента ТО. Новые технологии вводятся не просто для повышения какой-то одной характеристики по сравнению с аналогичным оборудованием – они применяются только после «обкатки» и удешевления настолько, насколько их использование будет экономически оправданным.
Применение современных технологий упрощает эксплуатацию, техническое обслуживание и ремонт. Предприятие может рекомендовать вариант, при котором один простой компонент двигателя можно заменить дважды, тем самым снизив износ более сложной детали и отложив ее замену.
Все технологии компания Guascor применяет с позиций их целесообразности. Как уже описывалось выше, можно использовать технологии, которые более затратны, чем совокупный результат от их применения. Как это выражается в конкретных цифрах? Предположим, что некая «новая технология» позволяет повысить электрический КПД электростанции на 0,5 %. При этом ее использование увеличит стоимость оборудования на Х, а суммарные затраты на эксплуатацию – на Y.
В финансовом выражении 0,5 % КПД – это значит, что для выработки того же объема электроэнергии понадобится газа примерно на 3,55 м3/ч меньше (экономия 17,75 р./ч). За 60000 часов экономия составит 1 млн рублей. Таким образом, если (X+Y)>1 млн рублей, использование данной технологии экономически нецелесообразно.
Нужно также помнить, что любые изменения за счет конструкции двигателя, технологий или материалов, которые позволят выиграть 0,5 % электрического КПД, также могут привести к потере эффективности утилизируемого тепла. Тепловая нагрузка, например, перейдет с охлаждаемой части на деталь, охлаждение которой более затруднительно и, соответственно, полезная теплоотдача системы когенерации будет ниже. Кстати, использование именно этой условной детали и повлечет за собой удорожание, о котором сказано выше.
В качестве конкретного примера – конструкционное решение системы когенерации с использованием промежуточного теплообменника рубашки охлаждения двигателя. Охлаждающая жидкость рубашки через такой теплообменник передает тепло из одного замкнутого контура в другой, который, в свою очередь, передает тепло на клиентский теплообменник. С одной стороны, данное решение делает систему более надежной, а с другой – более сложной, увеличивает конечную стоимость и снижает полезную теплоотдачу.
В заключение необходимо отметить, что применение того или иного оборудования оправданно лишь после тщательного расчета всего жизненного цикла эксплуатации энергоблока: стоимости, топлива, обслуживания, ремонтов и т.д. Таким образом, продукция Guascor – это разумная стоимость и экономичная эксплуатация, прозрачная и предсказуемая структура расходов заказчика. 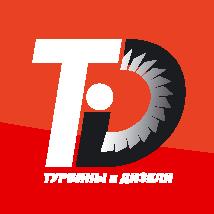