Квириджн Эппинга, Йос Ван Буйджтенен – Triogen B.V.
В последние годы стремление к максимальному использованию сбросного тепла различных процессов заметно повысилось. Оптимальный вариант – использовать это тепло для систем центрального отопления жилых домов и районов. Но для этого нужно, чтобы такой потребитель находился в непосредственной близости к источнику тепла. Однако температура сбросного тепла часто превышает ту, которая необходима для систем центрального отопления, следовательно, значительная часть энергии теряется. Также очень часто необходимость в отоплении ограничена.
Использование сбросного тепла для выработки электроэнергии позволяет передавать эту энергию потребителю, при этом эмиссия вредных веществ практически отсутствует. По этой причине разрабатываются небольшие электростанции, основанные на принципе органического цикла Ренкина (ORC).
В статье представлены результаты разработки и эксплуатации установок ORC компании Triogen. Работы по их созданию начались в 1990-х годах в Техническом университете г. Лаппеенранта в Финляндии. Пилотная установка была введена в опытно-промышленную эксплуатацию в 2002 г. в Нидерландах компанией Triogen B.V. [1]. В 2006 г. началось серийное производство установок ORC и поставка их заказчику. На данный момент создано 25 установок: 15 из них работают, 10 – на этапе ввода в эксплуатацию на объектах заказчиков.
Конструкция установки ORC
Ранее предпринималось множество попыток создания экономически выгодной системы, то есть системы, способной окупить вложенные средства в приемлемый срок. Но в связи с невысокими ценами на электроэнергию и доступными на тот момент технологиями эти попытки терпели неудачу, так как установки ORC были слишком дорогими. Для преодоления этого необходимо было обеспечить высокий КПД установок и оптимальную окупаемость системы. Температура процесса в цикле ORC является определяющим фактором:
во-первых, для достижения высокого КПД цикла Карно, во-вторых, для сокращения площади нагрева, необходимой для передачи энергии сбросного тепла рабочей жидкости системы.
Изначально установки компании Triogen были сконструированы для утилизации сбросного тепла выхлопных газов ГТУ и двигателей внутреннего сгорания. Температура выхлопных газов ниже необходимой температуры пара (540 °C) для паровых турбин, но достаточно высокая для того, чтобы обеспечить оптимальный КПД цикла Карно.
Для эффективной утилизации сбросного тепла нужно было найти химически устойчивую жидкость с критической точкой, примерно равной минимальной температуре источника. Длительное время для этой цели использовался фреон-114, затем он был запрещен в связи с негативным влиянием на озоновый слой. В качестве альтернативной рабочей жидкости использовался толуол, который является химически стабильным при максимальной температуре источника тепла и имеет приемлемую для различных систем, использующих цикл ORC, термодинамическую диаграмму.
Основываясь на этих показателях, было решено увеличить мощность установки ORC для утилизации сбросного тепла выхлопных газов газопоршневых энергоблоков в диапазоне от 1500 кВт. Энергоблоки такой мощности наиболее часто применяются в составе когенерационных установок, работающих на природном газе, биогазе, газе мусорных свалок и других видах газа.
Термодинамические данные, полученные в результате исследований по оптимизации цикла ORC с рекуператором, были использованы для достижения максимальной мощности установки. Температура конденсации рабочего тела в конденсаторе обеспечивается на минимальном уровне в зависимости от температуры окружающей среды. На рис. 1 представлена схема цикла и диаграмма T-s процесса. Рабочая жидкость подается из резервуара в основной насос, который установлен на одном валу с турбиной и высокооборотным генератором. Затем с максимальным рабочим давлением она подается в рекуператор и далее в испарительный теплообменник. Сбросное тепло направляется через испаритель, где рабочая жидкость нагревается до кипения, испаряется и перегревается. Хотя для эффективной работы установки перегрев рабочего тела не требуется, он необходим для контроля и компенсации потерь тепла между испарителем и турбиной.
В турбине рабочее тело расширяется, что приводит в действие высокооборотный генератор и главный насос. После расширения остаточная тепловая энергия рабочей жидкости используется в рекуператоре для предварительного нагрева рабочей жидкости перед подачей в испаритель. Под рекуператором расположен конденсатор, где пар конденсируется охлаждающей жидкостью перед тем, как рабочая жидкость поступит в емкость для хранения. В табл. содержатся основные термодинамические показатели, которые могут варьироваться в зависимости от параметров источника тепла.
Конструкция основных компонентов
Высокооборотный турбогенератор HTG
Самая интересная часть схемы цикла, представленной выше, – это комбинация турбины, генератора и насоса. Такая комбинация позволяет создать полностью герметичную систему. В этом случае нет никаких внешних соединений, следовательно, не нужны дополнительные материалы, обеспечивающие их уплотнение. Смазка деталей осуществляется рабочей жидкостью; генератор охлаждается рабочей жидкостью в жидком и газообразном состоянии. Такая особенность конструкции установки обеспечена благодаря генераторам, частота вращения которых соответствует оптимальной частоте силового вала турбины. В связи с этим нет необходимости в применении редуктора. Таким образом, обеспечивается высокая эффективность расширения рабочего тела при использовании одноступенчатой радиальной турбины. Это относится и к главному насосу, имеющему простую конструкцию. Еще одно преимущество расположения насоса на том же валу, что и другие компоненты, – это уникальная возможность контроля мощности, о чем будет рассказано далее.
Поскольку для смазки компонентов и охлаждения генератора используется одна рабочая жидкость, циркулирующая в высокооборотном турбогенераторе HTG, отдельная система охлаждения не применяется. Кроме того, устранена необходимость разделения рабочей жидкости и смазывающей жидкости. Внешние соединения корпуса HTG обеспечиваются фиксированными фланцевыми соединениями.
Частота вращения генератора составляет 28 000 об/мин, однако оптимальная рабочая частота обычно 25 000 об/мин. Гидродинамические подшипники имеют конструкцию с наклонными фланцами, которые подтвердили свою высокую надежность. Вал расположен вертикально, с насосом сверху и турбиной снизу, откуда отработанное газообразное рабочее тело направляется в рекуператор и конденсатор, а затем в емкость для хранения рабочей жидкости.
Для соединения высокооборотного генератора с компонентами статической системы применяются простые фланцевые соединения и гибкие рукава, что позволяет быстро демонтировать блок HTG для технического обслуживания и ремонта.
Испаритель
Конструкция испарителя довольно простая: он состоит из горизонтальных U-образных труб, фиксированных с одной стороны для расширения. Трубы малого диаметра изготовлены из нержавеющей стали, обеспечен легкий доступ для их очистки. Предельно допустимая температура рабочей жидкости выше температуры источника тепла, таким образом, испаритель надежно защищен от повреждений в связи с отсутствием потока. Стандартная конструкция может быть разных размеров, в зависимости от условий эксплуатации, объема и температуры источника тепловой энергии.
Выхлопные газы направляются вертикально, сверху вниз через испаритель. Наименьшая температура достигается в низшей точке, где осуществляется отбор конденсата.
Рабочая жидкость проходит по трубам в вертикальном направлении снизу вверх, в прямоточном режиме. При этом отсутствует необходимость в сепараторе, устранены все возможности утечки рабочей жидкости и попадание ее в турбину.
Рекуператор и конденсатор
Рекуператор предназначен для того, чтобы утилизировать остаточное тепло отработанной рабочей жидкости после расширения. Тепло передается рабочей жидкости под давлением, когда она поступает из конденсатора. Система сконструирована таким образом, что температура жидкости при ее поступлении в испаритель достаточно высока, чтобы избежать конденсации выхлопных газов, которые могут содержать серу.
И рекуператор, и конденсатор имеют компактные размеры. Они объединены с емкостью хранения рабочей жидкости в единый заводской модуль и являются основным блоком установки ORC. Емкость для хранения рабочей жидкости имеет индикатор уровня, состояние жидкости в конденсаторе постоянно проверяется на попадание туда неконденсируемых газов. Тепло, образующееся в результате конденсации, отбирается охладителем (обычно водой или водно-гликолевой смесью).
В случаях, когда доступен потребитель тепла, полученное тепло может эффективно использоваться. Для этого была разработана специальная модификация установки WB1Vario, где из конденсатора может отбираться тепло определенной температуры (до 80 °C). Конечно, отбор тепла будет осуществляться в ущерб электрической мощности установки, но система контроля обеспечивает оптимизацию ее эксплуатации в режиме реального времени и определяет, какой режим будет наиболее эффективным в каждый конкретный период работы.
Силовая электроника и управление
Для подсоединения высокооборотного генератора к сети (50 или 60 Гц) применяется инвертер, обеспечивающий прямое соединение трех фаз при напряжении 400 В. Сеть используется для пуска установки, частота вращения генератора постоянно контролируется в зависимости от необходимой температуры рабочей жидкости на входе в турбину. При этом важную роль играет комплексная конструкция модуля турбины, генератора и насоса.
Изменение подачи тепла в испаритель ведет к колебанию температуры рабочей жидкости. Контроллер изменяет частоту вращения генератора и, соответственно, турбины и насоса таким образом, что расход рабочей жидкости оптимизируется, обеспечивая заданную температуру на входе в турбину. В результате достигается плавная работа установки на всех режимах, вплоть до снижения нагрузки до 25 % от номинальной. Практически на всех режимах поддерживается КПД на уровне 60 %.
Силовая электроника и PLC-контроллер смонтированы в отдельном модуле, который на конкретных площадках эксплуатации может соединяться с аналогичными модулями других установок.
Энергетическая установка ORC мощностью 160 кВт
После успешных испытаний прототипа была разработана первая коммерческая установка WB1, которая состоит из 4 основных модулей для поставки под ключ [2]:
• стандартный технологический модуль, включающий высокооборотный турбогенератор HTG, рекуператор, конденсатор, емкость для рабочей жидкости, насос, клапаны, а также соединительные трубы и контрольно-измерительное оборудование;
• модуль подачи тепла: испаритель, отрегулированный для работы в соответствии с параметрами доступной тепловой энергии. Модуль подсоединяется к источнику тепловой энергии;
• модуль отвода тепла: плоские охладители охлаждающей воды для конденсатора, отрегулированного в зависимости от атмосферных условий конкретной площадки;
• стандартный модуль электроавтоматики, куда входят модуль регулирования параметров электроэнергии, который напрямую соединяет высокооборотный генератор с сетью, чтобы обеспечить напряжение 400 В, три фазы, частоту 50/60 Гц; модуль контроля и управления установкой ORC; независимая система безопасности.
Технологический модуль
Технологический модуль – это стандартный блок заводской сборки, его размеры соответствуют транспортировочным стандартам. Модуль включает рекуператор, конденсатор, емкость для хранения рабочей жидкости. Компоненты расположены вертикально и установлены в стальной каркас со специальными покрытиями и герметичными дверями. Высокооборотный генератор размещен в верхней части модуля таким образом, чтобы выходной поток из турбины направлялся вниз к емкости для хранения рабочей жидкости. Используются 4 основных канала соединения с другими модулями:
• жидкость и пар – в испаритель;
• охлаждающая жидкость – к плоскому охладителю или потребителям на площадке;
• электрические кабели – к инвертеру мощности;
• соединения для измерительной аппаратуры и системы управления – к модулю контроля.
Кроме основных соединений, могут использоваться система труб для вентиляции пэкиджа и выходные каналы аварийных клапанов.
Интеграция установки ORC в состав электростанции
На рис. 2 показана интеграция энергоблока ORC в состав электростанции с двумя биогазовыми двигателями мощностью по 800 кВт. В центре расположен технологический модуль. Модуль подачи тепла (испаритель) соединен с выхлопными трубами двух газовых двигателей с помощью системы труб и клапанов, чтобы обеспечить различные режимы работы (с одним или двумя двигателями), а также для отключения установки ORC от работающих двигателей в случае ее выхода из строя. Все блоки представляют собой конечные устройства. Установка не оказывает никакого воздействия на работу двигателей, обеспечивающих функциональность цикла ORC.
Варианты применения
Несмотря на то что первоначально установки ORC создавались для утилизации сбросного тепла выхлопных газов двигателей, они могут использоваться и для других целей, например, для сжигания биомассы и использования сбросного тепла производственных процессов (на мусоросжигательных заводах). Высокие температуры отходящих газов обеспечивают ряд преимуществ: тепло может передаваться рабочей жидкости без применения промежуточной жидкости или термальных масел. Это упрощает процесс, уменьшает потребление энергии таких систем, а также их стоимость. Однако можно использовать отходящие газы с низкими температурами, в частности, для нужд центрального отопления.
Таким образом, выделяемое тепло можно использовать при любых температурах: высокие температуры для производства электроэнергии, низкие – для обеспечения потребителей теплом, тем более система управления позволяет выбрать оптимальный на данный момент режим. На рис. 3 показан стандартный вариант применения установки ORC, а также эксплуатационные параметры Triogen ORC при взаимодействии с другими энергоблоками. Возможные варианты применения:
• газовые двигатели, работающие на природном газе, биогазе, газе мусорных свалок и шахтном метане;
• дизельные двигатели;
• газовые турбины малой мощности;
• когенерационные электростанции для тепличных хозяйств, систем центрального отопления;
• сжигание биомассы, древесных и бытовых отходов [3, 4];
• факелы для газа мусорных свалок или других промышленных газов;
• утилизация сбросного тепла на химических, металлургических, стеклотарных и деревообратывающих предприятиях.
Установки, введенные в коммерческую эксплуатацию
После более 4000 часов успешной работы прототипа компания Triogen ввела в 2007 году в коммерческую эксплуатацию первую установку ORC в составе когенерационной электростанции тепличного хозяйства на базе газопоршневого энергоблока Deutz мощностью 2 МВт. Затем были введены еще 19 установок, общая наработка которых к настоящему моменту составляет 200 000 часов. Показатель надежности установок составил 97 %. Наработка пилотной установки – более 36 000 часов. Перечень установок ORC, которые находятся в эксплуатации (по состоянию на март 2015 г.), приведен ниже:
• с газопоршневыми двигателями на биогазе: 7 установок в Нидерландах, 2 – в Чехии;
• с газопоршневыми двигателями на газе мусорных свалок: 2 установки во Франции, 2 – в Португалии, 1 – в Германии;
• с газопоршневыми двигателями на шахтном метане: 1 установка в Чехии;
• прямое сжигание газа мусорных свалок: в Нидерландах (прототип), во Франции – дополнительное сжигание за газопоршневыми двигателями;
• с газопоршневыми двигателями на природном газе: 1 установка в Нидерландах, использующая когенерацию;
• с биодизельными двигателями: 1 установка в Нидерландах;
• прямое сжигание твердой биомассы: 2 установки в Италии;
• проекты в стадии разработки: 10 установок для заказчиков в Бельгии, Германии, Чехии, Италии и Англии.
Заключение
Многоцелевая концепция установок ORC, разработанная специалистами Технического университета г. Лаппеентранта, была реализована компанией Triogen (Нидерланды), и в результате создан модельный ряд установок ORC в различных диапазонах мощности. Первая из них имела мощность 145 кВт, следующая модификация – 165 кВт. В дальнейшем планируется вывод на рынок установок в диапазоне 60…170 кВт.
Дальнейшие разработки по модификации установок направлены на оптимизацию динамики потока рабочей жидкости в турбине и насосе [5]. Будут расширены варианты применения. В частности, планируется использовать их для утилизации сбросного тепла металлургических и химических заводов, деревообрабатывающих комбинатов, а также для прямого сжигания биомассы и твердых бытовых и промышленных отходов.
Опыт эксплуатации установок ORC на объектах заказчиков подтвердил их высокую надежность, доступность и безопасность. 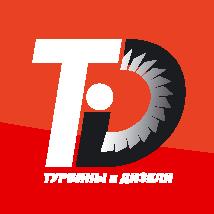
Использованная литература
1. Prof. ir Jos van Buijtenen, prof. J. Larjola et al: Design and validation of a new high expansion ratio radial turbine for ORC application, 5th European Conference on Turbo-machinery, Praha, March 2003.
2. J.P. van Buijtenen: The tri-o-gen organic Rankine cycle: development and perspectives, Power Engineer, Journal of the IDGTE, March 2009, Volume 13 Issue 1.
3. Heinimo, J.P. van Buijtenen, J. Larjola, J. Backman: Small electricity production with high speed ORC technology. International Nordic Bioenergy 2003 conference, Jyvaskyla, 2/5 September 2003.
4. Heinimц, J., van Buijtenen, J.P., Backman, J., Ojaniemi, A. & Malinen, H.: High-speed ORC technology for distributed electricity production, 2nd World Conference on Biomass for Energy, Industry and Climate Protection, 10-14 May 2004, Rome, Italy.
5. John Harinck, David Pasquale, Rene Pecnik, Jos van Buijtenen, Piero Colonna: Performance improvement of a radial ORC turbine by means of automated CFD design, 10th European Conference on Turbo-machinery, Lappeenranta, April 2013.
Статья подготовлена по материалам доклада, представленного на конференции PowerGen Europe ‘2014, Кельн (Германия)