Майкл Коун – RWE npower, Великобритания
Мотому Кунимицу – Mitsui Engineering & Shipbuilding Co., Ltd., Япония
Изотермический двигатель является комплексной системой, включающей в себя квазиизотермический воздушный компрессор, рекуператор и двигатель внутреннего сгорания. В перспективе КПД данного двигателя может достигать 60% при работе на очищенном жидком топливе и 58% – на природном или других высококалорийных газах.
Разработка и начальные испытания прототипа двигателя
Изодвигатель является новейшим высокоэффективным поршневым двигателем мощностью 2...20 МВт, который может применяться в составе электростанций или для судового привода. На основании результатов компьютерного моделирования предполагаемый КПД двигателя составит 55…60%. Достижение такого уровня эффективности на практике зависит от того, насколько успешными будут разработки необходимых компонентов и рабочих процессов.
Разработку изодвигателя и его компонентов начала в 1992 году компания National Power (Великобритания), реализацию проекта осуществляли Innogy и RWE npower. Испытания изотермического компрессора были успешно проведены в 1994-1995 гг. с использованием одного цилиндра конвертированного судового дизельного двигателя. Испытания камеры сгорания при работе на природном газе и жидком топливе (воздух подается с давлением 2,5 МПа при температуре 600...700°С) прошли в 1997 году на конвертированном судовом двигателе.
Прототип изодвигателя мощностью 3 МВт, известный как ED (Engineering Demonstrator – инженерная модель), был изготовлен и испытан на предприятии Ricardo Consulting Engineers в г. Шохэм (Великобритания) в 2001-2003 гг. В дальнейшем, в рамках договора о сотрудничестве между RWE npower и Mitsui Engineering & Shipbuilding Co., Ltd. (MES), он был перевезен в Японию для проведения дальнейших испытаний и доработки конструкции. Двигатель был установлен на предприятии MES в г. Тамано в 2004 году, где продолжились комплексные испытания. По их завершении собственность на технологии изодвигателя и изотермического компрессора перешла к MES.
Как и ожидалось, при проведении испытаний специалисты столкнулись с многочисленными проблемами. Однако в результате были получены необходимые данные и наработан обширный опыт, который использовался для дальнейшей доработки конструкции двигателя.
В статье обобщен опыт испытаний прототипа изодвигателя и проанализированы полученные результаты. Обсуждаются возможные направления доработки в отношении основных компонентов системы, таких как камера сгорания, система охлаждения, изотермический компрессор, трубная обвязка и теплообменники. Процесс сгорания в двигателе включает смешивание подогретого и сжатого воздуха с повторно сжатыми выхлопными газами и впрыскивание топлива в эту смесь. Данный процесс значительно отличается от процессов подготовки топлива в стандартных двигателях или двигателях с искровым зажиганием.
Важным направлением доработки является процесс запуска двигателя и вывод его на номинальную мощность. В прототипе двигателя используются электрические подогреватели воздуха, при этом рекуператор остается холодным. Обсуждается возможность доработки данной системы или замены ее альтернативной.
В связи с высокой тепловой нагрузкой, в конструкции прототипа изодвигателя применен ряд специфических компонентов. Это связано с тем, что двигатель работает по двухтактному циклу, при котором подаваемый воздух, уже горячий и сжатый, не может обеспечить достаточное охлаждение цилиндров. В статье даны предложения по контролю тепловой нагрузки без снижения термического КПД двигателя.
В процессе испытаний изотермический компрессор подтвердил свою надежность, однако и здесь необходим ряд доработок. Оптимизация конструкции компрессора является важным направлением, поскольку высокая степень сжатия обеспечит более высокую мощность без сжигания дополнительного количества топлива.
Принципы, положенные в основу изодвигателя
Одноцилиндровый изотермический компрессор и три цилиндра двигателя подсоединены к общему коленчатому валу. Для достижения квазиизотермальной компрессии большое количество распыленной охлажденной воды впрыскивается в компрессор в процессе такта сжатия. Распыленная вода полностью поглощает теплоту, образующуюся при сжатии, что обеспечивает необходимую низкую температуру воздуха даже при степени сжатия 25. Образование пара при этом отсутствует. Вода и сжатый воздух направляются из компрессора в сепаратор, где вода отделяется, охлаждается и поступает обратно в компрессор. Тепловая энергия выхлопных газов с помощью рекуператора используется для подогрева сжатого воздуха.
Избыточная теплота воздуха из турбонагнетателя и системы охлаждения двигателя может быть также утилизирована с помощью дополнительных теплообменников, расположенных между компрессором и рекуператором. Для утилизации избыточного тепла от системы охлаждения необходим впрыск небольшого количества воды в сжатый воздух после сепаратора. Водяной пар проходит через систему и затем выбрасывается в атмосферу – расход воды при этом примерно равен расходу топлива.
Цилиндры двигателя работают по двухтактному циклу, при котором предварительно сжатый и подогретый воздух подается в цилиндр через быстродействующий впускной клапан, когда поршень находится вблизи верхней мертвой точки. Затем впрыскивается топливо, начинается процесс горения, расширение и выпуск. Выпускные клапаны находятся на крышке цилиндра рядом с впускными клапанами. Поскольку выпускные клапаны закрываются до открытия впускных, продувки цилиндра не требуется.
Конструкция изодвигателя
Частота вращения силового вала двигателя должна быть достаточно небольшой, чтобы обеспечить необходимое время для передачи воде, которая впрыскивается в изотермический компрессор, теплоты сжатого воздуха. Максимальная частота вращения не должна превышать 600 об/мин при выработке электроэнергии с частотой 50 или 60 Гц.
В отличие от стандартного дизельного двигателя, подаваемый в цилиндр воздух не обеспечивает его охлаждения, поскольку он предварительно нагрет до 700°С. Температура выхлопных газов также достаточно высока (около 750°С), что обеспечивает возможность предварительного подогрева подаваемого воздуха. Все это создает высокую тепловую нагрузку в двигателе. С другой стороны, процесс горения в изодвигателе (в отличие от стандартного двигателя) происходит на другом угле поворота коленчатого вала, поэтому подаваемые в цилиндр газы быстрее расширяются. Это снижает максимальную температуру горения. Кроме того, впрыск воды в подаваемый воздух (с целью утилизации теплоты из системы охлаждения) также снижает температуру горения.
Поскольку воздух подается в цилиндры при высокой температуре, охлаждение камер сгорания двигателя должно осуществляться водяной системой охлаждения. В принципе, высокая тепловая нагрузка двигателя может контролироваться за счет оптимизации его конструкции, применения передовых материалов и выбора оптимальных параметров работы. При этом КПД двигателя существенно не снизится.
Расчеты по влиянию трех основных проектных параметров на тепловую нагрузку были представлены на конгрессе CIMAC-2004. Тепловая нагрузка при этом была определена как прогнозируемая максимальная температура поверхности поршня. Основными проектными параметрами были обозначены: температура подаваемого воздуха; рабочее давление; температура горения. Другие параметры, такие как частота вращения (600 об/мин), диаметр (370 мм) и ход (450 мм) поршня были оставлены неизменными. Средняя скорость движения поршня – 9 м/с. В качестве топлива использовалось дизельное топливо.
Расчеты показали, что снижение рабочего давления (с помощью турбонагнетателя с меньшей степенью сжатия) – это наиболее эффективный путь сокращения тепловой нагрузки без снижения КПД. При этом 20%-е снижение рабочего давления (15 до 12 МПа) обеспечивает сокращение максимальной температуры поршня на 40°С, а потери КПД составят всего 0,5%. Снижение температуры горения на 200°С (с 1700 до 1500°С) обеспечивает понижение максимальной температуры поршня на 45°С, а потери КПД при этом составят 1,5%. Быстро активировать ресурсы организма Вам помогут пантовые ванны , древняя методика проверенная веками Гораздо худшие результаты при снижении температуры подаваемого воздуха: при снижении ее на 100°С (с 750 до 650°С) КПД падает на 1,5%, а уменьшение максимальной температуры поршня составляет только 30°С.
Таким образом, оптимальными параметрами были определены: температура горения 1500°С, температура подаваемого воздуха 700°С, рабочее давление 12 МПа. При этом расчетный КПД составит 56%, а электрическая мощность изодвигателя с тремя рабочими цилиндрами и одним цилиндром компрессора – 2,35 МВт. Расчетная максимальная температура поверхности поршня – 740°С. Такая температура является слишком высокой для традиционных материалов головки поршня, но приемлема для сплава Nimonic (жаропрочный никелевый сплав).
Мощность двухтактного изодвигателя сопоставима с мощностью четырехтактного дизельного двигателя, учитывая произведение BMEP•MPS/RPPS, где ВМЕР – среднее эффективное давление; MPS – средняя скорость движения поршня; RPPS – количество оборотов вала за один такт (2 – для четырехтактного двигателя, 1 – для изодвигателя). Значение приведенной формулы для четырехтактного двигателя составляет 125, для изодвигателя мощностью 2,35 МВт – 153 (без учета цилиндра компрессора). На основе данного показателя видно, что мощность изодвигателя со сниженной тепловой нагрузкой будет на 22% выше, чем у стандартного двигателя.
Прототип изодвигателя мощностью 3 МВт
Прототип изодвигателя имел один цилиндр компрессора диаметром 385 мм и три рабочих цилиндра 370 мм, ход поршня у всех цилиндров – 400 мм. Максимальное рабочее давление – 10 МПа. В составе ED дополнительно используется электрический воздухонагнетатель для повышения давления в изотермическом компрессоре на 0,8 МПа. Его применение увеличивает мощность двигателя, но при этом повышается тепловая нагрузка и снижается расчетный КПД.
Электрический воздухонагнетатель расположен за турбонагнетателем, а изотермический компрессор – рядом с блоком предварительного подогрева подаваемого воздуха, где воздушный поток разделяется и утилизируется тепло от теплообменников и двух систем охлаждения двигателя. На данной схеме показаны две отдельные системы охлаждения изодвигателя ED (низко- и высокотемпературная), хотя в дальнейшем возможно использование единой системы.
Два воздушных потока объединяются и проходят через рекуператор, где утилизируется тепло выхлопных газов. Проектная температура подогретого газа – 750°С. После процесса горения выхлопные газы с давлением до 0,5 МПа проходят через первую ступень рекуператора, а затем направляются в турбонагнетатель. Окончательная температура выхлопных газов перед выбросом в атмосферу составляет 125°С.
Размеры (ДхШхВ) изодвигателя ED составляют 8x5x6 м. На правой стороне двигателя расположена система HVAS (Hydrolic valve actuation system – гидравлическая система управления клапанами), которая приводит в действие впускные клапаны рабочих цилиндров. Система обеспечивает ED необходимую гибкость при проведении испытаний, однако для двигателя, который будет представлен на рынок, она не предусмотрена, так как потребляет слишком много энергии. Цилиндр компрессора расположен на стороне присоединения генератора – за маховиком, рядом с сепаратором. Динамометр гидравлического тормоза находится на другой стороне генератора.
Изотермический компрессор
Изотермический компрессор имеет три обычных кулачковых впускных клапана и четыре отсечных клапана, которые расположены на крышке цилиндра. Клапаны открываются в направлении от цилиндра. Отсечные клапаны приводятся в действие в том случае, если давление в цилиндре выше, чем в выпускном канале.
В состав напорной системы нагнетания для впрыска воды входят накопитель, высоко- и низконапорная системы подачи воды, золотниковые клапаны, которые открываются при сжатии и закрыты в процессе такта всасывания.
Контроль работы пяти золотниковых клапанов осуществляет оператор двигателя. Два клапана, расположенные на противоположной стороне компрессора, контролируют поток к двум коллекторам. Пятый клапан находится на низконапорной цепи, но во время испытаний он был закрыт. Золотниковые клапаны оказались слишком большими, чтобы приводиться в действие электрическими соленоидами, поэтому были применены гидравлические (с использованием воды вместо масла). На пилотном двигателе клапаны имели электропривод, так как были достаточно малы.
Два коллектора спроектированы в форме круговых (водораспределительных) колец, оснащенных форсунками. Каждое кольцо имеет два ряда форсунок – по 90 в каждом ряду. Угол распыления у форсунок верхнего и нижнего коллектора 32° и 100° соответственно. Форсунки нижнего коллектора обеспечивают больший объем распыления. Направление форсунок различно для каждого ряда, причем у форсунок нижних рядов наклон больше.
Компрессор двигателя имеет поршень с алюминиевым покрытием с поршневыми кольцами PTFE (polytetrafluoroethylene – тефлон). Для охлаждения и смазки используется впрыск воды. Поскольку температура компонентов компрессора не превышает 100 °С, нет необходимости изготавливать их из термостойких материалов. Компрессор имеет крейцкопфную конструкцию с фонарным кольцом уплотнения на штоке поршня для отделения смазочного масла картера двигателя от впрыскиваемой воды. Любая утечка масла или воды устраняется с помощью уплотнения.
Теплообменники и рекуператор
Турботеплообменник, низко- и высокотемпературные теплообменники охлаждения двигателя, а также теплообменник для охлаждения впрыскиваемой воды кожухопластинчатого типа изготовлены компанией Vahterus (Финляндия). Все теплообменники, использованные в составе изодвигателя, разработаны для работы при давлении 10 МПа.
Кожухопластинчатый теплообменник совмещает в себе все преимущества пластинчатого и кожухотрубчатого теплообменника и является надежным, компактным устройством без уплотнений. Кроме того, он обладает высоким коэффициентом теплопередачи и стойкостью к высоким температурам и давлению. Сердцевиной теплообменника является полностью сварная кассета круглых пластин, помещенная во внешний кожух.
Рекуператор изодвигателя ED разработан компанией Mitsui-Babcock для обеспечения подогрева подаваемого воздуха до 800°С с давлением 0,5 МПа. Температура выхлопных газов на выходе составила 270°С, падение давления с газовой стороны – не более 10 кПа. При испытаниях рекуператор обеспечил подогрев воздуха до 750°С при давлении 10 МПа, падение давления с воздушной стороны не превысило 0,15 МПа.
Электрические подогреватели воздуха
Электроподогреватели используются для подогрева 12 параллельных труб NF709, которые подают воздух от рекуператора к рабочим цилиндрам. Трубная обвязка NF709 разработана таким образом, чтобы эффект теплового расширения был компенсирован эластичностью труб. Подогреватели состоят из проводов высокотемпературного сопротивления, соединенных керамическими элементами вокруг труб.
Всего использовалось 48 электрических подогревателей (длиной по 880 мм) – по четыре на каждую трубу. Пучок труб с подогревателями был укрыт теплоизоляционными материалами. Внутренняя теплопередача между горячими трубами и воздухом усиливалась за счет использования проволочной спирали на внутренних стенках труб. В процессе испытаний на стендах компании Mitsui-Babcock был подобран оптимальный диаметр проволоки. Все подогреватели были оснащены термопарами для измерения температуры металла труб, но показания снимались только с 24 подогревателей. Показания термопар остальных подогревателей оказались аналогичными, поэтому в дальнейшем их мониторинг не проводился.
Коллектор подаваемого в камеру сгорания воздуха
С помощью параллельных труб NF709 сжатый и подогретый воздух подается к трем входным коллекторам. Их назначение – обеспечить достаточное количество воздуха для подачи в цилиндр, чтобы избежать резкого падения давления в нем. Входные коллекторы подсоединены к впускным клапанам каждого из трех рабочих цилиндров через сильфонные блоки.
Для воздушных коллекторов и сильфонных блоков использована внутренняя теплоизоляция. Она состоит из керамических волокон, защищенных тонким листом нержавеющей стали. Термоизоляционный слой находится между стенкой трубы, выполненной из хромированной стали, и тонкой внутренней прокладкой из сплава Haynes. Допустимая температура внешних стенок труб составляет 250°С.
Рабочие цилиндры
Сжатый и подогретый воздух подается в цилиндры через два впускных клапана, которые открываются наружу. Это необходимо для того, чтобы избежать контакта с поршнем (удара) при впуске воздуха в верхней мертвой точке (TDC), учитывая, что конструкция цилиндра обеспечивает минимальное «вредное» пространство. Гидравлическая система управления клапанами позволяет оператору настраивать открытие и закрытие клапанов при любом угле поворота коленчатого вала (СА).
Каждый рабочий цилиндр имеет также два выпускных клапана тарельчато-кулачкового типа, которые открываются внутрь цилиндра. Впускные и выпускные клапаны выполнены из композитных материалов (хромокремниевых сплавов), крышки цилиндра – из сплава Nimonic 80А для обеспечения максимальной термо- и износостойкости. Внутреннее охлаждение применяется как для впускных, так и для выпускных клапанов с целью эффективного отвода тепла от седла каждого из клапанов.
Никелевые сплавы использовались для головок поршня, компонентов горячей части, а также для покрытия каналов впуска и выпуска. Калибровочное кольцо цилиндра выполнено из сплава Nimonic с включением керамических материалов, чтобы минимизировать деформацию гильзы цилиндра. Гильза цилиндра, центробежно-литая из серого чугуна, имеет усиленную конструкцию, со спиральными охлаждающими каналами, расположенными максимально близко к внутренней поверхности. Крышка цилиндра также выполнена из серого чугуна. Для подбора оптимальных материалов, оптимизации конструкции цилиндров и систем охлаждения использовались программы компьютерного анализа CFD (численные методы гидро- и газовой динамики) и FEA (метод конечных элементов).
Охлаждение компонентов горячей части осуществляется по высокотемпературному контуру; охлаждение гильз цилиндров, седел клапанов и крышек цилиндров – по низкотемпературному. Для впрыска топлива через центральную форсунку используется система подачи Common Rail. Форсунки могут быть настроены таким образом, чтобы производить до 4 коротких впрысков топлива на каждый оборот вала. Продолжительность и частота впрысков, давление топлива при впрыске также регулируются.
Запуск двигателя и выход на номинальную мощность
Сначала осуществляется подогрев трубной обвязки NF709 стационарного двигателя электрическими подогревателями. После того как температура труб достигнет 500°С, двигатель запускается с частотой вращения 200 об/мин с помощью электростартера – изотермический компрессор начинает подавать воздух. На начальном этапе впускные клапаны открыты, давление в рабочих цилиндрах низкое. Горячий воздух подается по горячим трубам в воздушный коллектор.
Когда температура на входе в рабочий цилиндр достигнет 350°С, впускные клапаны начинают работать – открываются при 35° и закрываются при 90° после верхней мертвой точки. Впускные и выпускные клапаны закрываются в положении между углом поворота коленчатого вала 35° и верхней мертвой точкой таким образом, что около 17% газа, который подан в цилиндр при нахождении поршня в нижней мертвой точке (BDC), удерживается и сжимается поршнем. Объем цилиндра при нахождении поршня в TDC составляет всего 3,2% от его объема при нахождении в BDC. Степень сжатия составляет при этом 14.
Давление в системе быстро растет, что обеспечивается частотой открывания впускных клапанов. Впрыск воды в компрессор начинается при давлении 0,4 МПа и частоте вращения двигателя 400 об/мин. Электрический воздухонагнетатель также приводится в действие. При повышении давления в системе расширение газа при горении вызывает охлаждение выхлопных газов. Необходимо постепенно увеличивать подачу топлива для поддержания температуры выше 200°С. Если данное условие не будет обеспечено, могут возникнуть трудности с розжигом топливовоздушной смеси.
Когда давление в системе достигает 2 МПа, подачу топлива нужно увеличивать с целью повышения температуры выхлопных газов, чтобы рекуператор обеспечил необходимый подогрев подаваемого воздуха. На данной стадии (которая не была достигнута на практике) воздушные подогреватели могут быть отключены. Дальнейший рост мощности возможен за счет повышения частоты вращения двигателя, а также повышения давления с помощью турбонагнетателя. 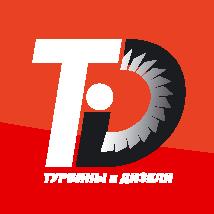
Конец 1-й части