С. П. Федулов – компания ETW Energietechnik GmbH
Перспективы развития децентрализованного энергоснабжения в России и высочайший интерес частных инвесторов к данной отрасли сегодня высоко оцениваются зарубежными производителями энергетического оборудования, побуждая их к активному присутствию на отечественном рынке.
Проект по созданию энергоцентра собственных нужд на комбикормовом заводе холдинга «АгроПромкомплектация» в Курской области успешно реализован компанией ETW Energietechnik GmbH в сотрудничестве с российскими партнерами. Заказчиком проекта выступило подразделение холдинга – «АгроПромкомплектация – Курск», развивающее в регионе свиноводческое и зерновое направление. Предприятие возводит ряд крупных свиноводческих ферм, для обеспечения которых в Конышевском районе Курской обл. решено было построить собственный промышленный комплекс (ПК), включающий комбикормовое производство, рассчитанное на ежесуточную выработку 600 т кормов, и элеватор для хранения 102 тыс. т зерна.
При проектировании ПК учитывались основные задачи – снижение себестоимости выпускаемой продукции и повышение рентабельности производства. Предлагалось минимизировать энергозатраты путем внедрения собственных генерирующих мощностей на предприятии. Это обусловливалось и техническими возможностями, и состоянием электросетей централизованного поставщика энергии в данном районе.
Необходимо было также обеспечить основное оборудование – грануляционную установку комбикорма – паром требуемого объема и качества, а также удовлетворить потребности всего объекта в теплоснабжении. В результате принимается решение о строительстве миниТЭС электрической мощностью 2400 кВт и тепловой – 1200 кВт на базе газопоршневых энергоблоков. Для удовлетворения технологических потребностей требовалось оборудование производительностью 2500 кг/ч насыщенного пара температурой 170 °С и давлением 0,8 МПа. Предполагалась параллельная работа энергоцентра с сетью ОАО «МРСК Центра» – «Курскэнерго».
Реализация проекта началась в июне 2011 года. Компания ETW Energietechnik выполнила техническое задание на проектирование генерирующего оборудования. В его состав вошли три когенерационные установки (КГУ) собственного производства ETW800EG электрической мощностью по 800 кВт и тепловой – по 856 кВт с газовыми двигателями MWM TCG2016V16C.
Выработку пара должны обеспечивать две парогенераторные установки общей производительностью не менее 2500 кг/ч. При этом расчет делался на максимально возможное использование тепловой мощности КГУ путем утилизации тепла отработавших газов двигателей. Это было связано с достаточно высокой теплоотдачей выхлопных газов двигателя TCG2016V16C, составляющей 449 кВт при температуре отходящих газов 457 °С. Отработавшие газы должны подаваться по газоходам, ведущим от двух двигателей КГУ, в двухтяговый дымогарный паровой котел-утилизатор (им комплектовалась одна из парогенераторных установок) тепловой мощностью 660 кВт и паропроизводительностью 966 кг/ч.
Третья КГУ подключалась через линию отвода отработавших газов к гибридному котлу другой парогенераторной установки – дымогарножаротрубному, который оснащался газовой горелкой Weishaupt WM-G20 мощностью 1600 кВт. Тяга отработавших газов котла позволяла производить еще 502 кг/ч насыщенного пара – в совокупности это составляло 1468 кг/ч за счет утилизации тепла отработавших газов. Недостающее количество вырабатывалось за счет газовой горелки максимальной производительностью 2500 кг/ч, что позволяло получать пар в требуемом объеме независимо от количества утилизируемых газов. Остальную тепловую мощность КГУ от утилизации тепла, образующегося в системе охлаждения двигателя (407 кВт на каждый агрегат), планировалось использовать для теплоснабжения предприятия.
Поскольку ПК создавался на неосвоенной площадке, то в целях минимизации расходов на общестроительную часть, сокращения сроков на монтаж и ввод энергоцентра в промышленную эксплуатацию все оборудование должно иметь контейнерное исполнение.
Проектировщиком и изготовителем парового котельного оборудования и его автоматики выступила немецкая фирма Achenbach GmbH, имеющая большой опыт в данной области. Контейнерные парогенераторные установки, включая всю соединительную часть между КГУ и котлами: газоходы, арматуру, дымовые трубы и байпасы отработавших газов, – изготовила компания ETW Energietechnik. Двигатели TCG2016V16C произведены на заводе MWM GmbH, сами же энергоустановки ETW800EG – от проектно-конструкторской разработки до полного изготовления – являются продуктом ETW Energietechnik.
Одновременно с разработкой и изготовлением энергооборудования решались не менее актуальные задачи проектирования энергоцентра вместе с наружными и внутренними сетями газои теплоснабжения. Для этого были привлечены отечественные проектные и инжиниринговые компании. Так, генпроектировщиком всего энергоцентра выступило ЗАО «СЭГ–Холдинг» (г. Курск), которое также выполнило инжиниринговые работы – монтаж комплекса утилизации тепла, поступающего от КГУ, наружные сети газоснабжения, узлы коммерческого учета газа, инженерные сети и коммуникации. Внешний узел утилизации тепла обеспечивал передачу тепловой мощности КГУ через внешние теплообменники на отопление административно-бытовых помещений и производственного корпуса комбикормового цеха. Параллельно с когенерационными установками работает поставленная компанией пиковая котельная мощностью 300 кВт.
ЗАО «СЭГ–Холдинг» также спроектировало, поставило и смонтировало станцию водоподготовки для парогенераторных станций производительностью 2,5 т/ч с резервом хранения 5 тонн и блочную станцию деаэрированной питательной воды.
Реализацию данного проекта: поставку, таможенное оформление, монтаж и пусконаладку оборудования в установленные контрактом сроки – осуществляло российское представительство компании ETW Energietechnik. Ввод энергоцентра в промышленную эксплуатацию состоялся в июне 2012 года на торжественном открытии всего производственного комплекса. Сегодня собственные генерирующие мощности компании «АгроПромкомплектация–Курск» полностью обеспечивают электричеством, теплом и паром производственную площадку элеватора и комбикормового цеха, а проект уже признан заказчиком экономически целесообразным.
Модуль когенерационной установки
Установки ETW800EG созданы на базе эффективного двигателя TCG 2016 V16С механической мощностью 826 кВт. Двигатель имеет высокие технические показатели, в т.ч. механический и электрический КПД (43,6 % и 42,2 % соответственно), а также низкие эксплуатационные расходы: экономичный расход топливного газа (189,5 м3/ч) и моторного масла (0,2 г/кВт·ч), повышенный ресурс до капитального ремонта – 64000 моточасов.
Выработка электроэнергии осуществляется синхронным генератором Marelli MJB 400 LС 4 номинальной электрической мощностью 800 кВт, соединенным через муфту сцепления с приводным двигателем. Силовой агрегат располагается на общей опорной стальной раме, которая устанавливается на амортизирующих опорах.
Система охлаждения двигателя интегрирована в общий высокотемпературный контур нагрева КГУ. Это позволяет циркулирующей воде осуществлять теплоотбор с рубашки охлаждения двигателя, турбокомпрессора выхлопных газов, масляной системы, а также из системы охлаждения газовоздушной смеси, нагревая внешнюю сетевую воду через пластинчатый передаточный теплообменник. Температура на входе в теплообменник составляет 70 °С, на выходе – 85 °С.
Для требуемого охлаждения двигателя через него постоянно перекачивается определенный объем воды с заданной температурой. Поскольку контур нагрева является комбинированным с системой охлаждения, то в случае полного потребления тепла вода в теплообменнике охлаждается до необходимой температуры на входе в двигатель (84 °С). При недостаточном для охлаждения воды разборе тепла в системе открывается контур резервного охладителя. В каждом случае система охлаждения функционирует путем пропорционально-интегрального регулирования оборотов насоса охлаждающей жидкости двигателя, трехходовых сервоприводов и вентиляторов резервного охладителя, чтобы поддерживать постоянный объем и заданную температуру охлаждающей жидкости с минимальными энергозатратами.
Масляная система агрегата оснащена дополнительным циркуляционным баком на 200 литров для увеличения интервалов замены масла. Подпитка системы маслом осуществляется из резервуара с запасом чистого масла 1000 л, для слива отработанного масла также имеется резервуар объемом 1000 л. Станция резерва моторного масла пополняется через пистолет для заправки масла из внешних емкостей.
Каждая энергоустановка оснащена системой общестанционного управления на базе программируемого контроллера Siemens – S7-300 с оригинальным программным продуктом VisuPro компании ETW Energietechnik. Интерфейс программы максимально прост и доступен для обслуживающего персонала, имеет богатый функционал.
Система управления TEM-Evo выполняет функции регулирования, контроля и визуализации для газомоторного агрегата и всех непосредственно относящихся к нему узлов установки. Компьютер системы оснащен 15-дюймовым графическим цветным LCD-дисплеем с сенсорным экраном. Между TEM-Evo и общестанционным управлением осуществляется связь по сетевому протоколу Profibus с индикацией основных параметров работы двигателя через интерфейс программы обслуживания ETW VisuPro.
Многомодульное исполнение энергоцентра потребовало его оснащения системой вышестоящего управления, регулирующей параметры каскадного подключения и отключение энергоблоков, распределение нагрузки, контроль и питание цепей безопасности парогенераторных установок. В меню вышестоящей системы управления также отображаются данные измерений внешней сети – напряжение и ток на фазах, активная и реактивная мощность, потребляемая из сети реактивная энергия, частота и cos(ф) сети. Эти данные в дальнейшем используются для управления параметрами синхронизации генератора с сетью.
Энергоблоки могут работать не только в параллель с сетью. В аварийных ситуациях, когда синхронизация невозможна, они автоматически переходят в островной режим работы, а при возобновлении питания возвращаются в параллельный режим. При этом управление сетевым выключателем, установленным в РУ заказчика, (в т.ч. его размыкание и замыкание) выполняется из вышестоящей системы управления агрегатами.
Все оборудование энергоблоков размещено в специальных 40-футовых расширенных контейнерах, разделенных на машинное отделение и отделение шкафов управления. В каждое отделение ведет отдельная огнестойкая дверь, с торцевой стороны машинного отделения располагаются двустворчатые ворота с модулями приточной вентиляции. Ширина контейнера составляет более 3 метров, что создает удобство обслуживания и эксплуатации установок. Контейнеры соответствуют классу огнестойкости F90. Исполнение стенок контейнера обеспечивает повышенное поглощение шума агрегата – до 68 дБ(A) на расстоянии 10 м. Для глушения шума выхлопных газов применяется комбинированный глушитель отражения и поглощения.
Электрические конвекторы поддерживают стабильную температуру в контейнере. В машинном отделении установлен двухступенчатый сигнализатор загазованности и детекторы дыма. Система подогрева воздуха на впуске позволяет эксплуатировать установку при температуре окружающего воздуха до –40 °С.
Котел-утилизатор отработавших газов
Тело котла выполнено горизонтальным, с большим водяным объемом. Дымовой газ поступает по дымогарным трубам, проходящим напрямую через тело котла. Трасса дымового газа окружена барабаном котла, в котором находится кипящая вода, паровое пространство располагается сверху. Благодаря большой поверхности воды и пространству для пара достигается исключительное качество пара при доле воды 1–2 %, в зависимости от давления в котле. Дополнительно в барабане установлен простой капельный сепаратор.
Чтобы питательная вода не попадала на горячие поверхности и не приводила к превышению точки росы (с опасностью возникновения коррозии), она поступает через распределительную трубу в барабан котла, обеспечивая хорошее смешивание с котловой водой. Большое пространство для воды в котле, что характерно для котлов-утилизаторов Achenbach, имеет весомые преимущества, в том числе значительное сглаживание колебаний между получением пара и поступлением теплоносителя. Кроме того, котел остается горячим даже при длительных отключениях, что исключает опасность коррозии от холодного пуска.
Отработавшие газы поступают по полностью разделенным газоходам, исключая взаимовлияние обоих потоков. Они сводятся на противоположной стороне котла в раздельных коллекторах и отводятся каждый через свой штуцер. Коллекторы оснащены большой общей дверцей, благодаря чему все газоходы доступны для чистки и проверки.
Котел оснащен всей необходимой арматурой, приборами контроля, устройством отбора проб воды, штуцерами для продувки котла, люками, предохранительными клапанами, а также отдельной питательной группой (насосы, грязеуловители, арматура). Для изоляции котла используются маты из минерального волокна, положенные на простеганное проволокой полотно и покрытые алюминиевыми листами. Толщина изоляции составляет 100 мм. Котел располагается на специальных опорах, позволяющих устанавливать его на горизонтальном, ровном фундаменте.
Котельная установка размещается в специальном 30-футовом контейнере. Контейнер парогенераторной установки расположен между контейнерами энергоблоков. Газоходы отработавших газов от двигателей КГУ имеют систему автоматических байпасов для обхода парогенератора при отсутствии необходимости в отборе пара.
Гибридный котел
Парогенераторная станция с гибридным котлом и горелкой также размещается в 30-футовом контейнере. Конструкция котла с дожиганием аналогична котлу-утилизатору: с одной стороны он имеет газоход дымогарной трубы, с другой – полностью изолированный дополнительный газоход жаровой трубы для сгорания газа. Указанные тяги парового котла полностью отделены друг от друга. Утилизируемое тепло не оказывает никакого влияния на пламя, благодаря чему может применяться серийная горелка для парового котла. Она используется для увеличения мощности вместе с утилизируемым теплом отработавших газов.
Жаротрубная часть состоит из большой жаровой трубы для полного и экологичного сгорания топлива, топочной камеры и трубопровода охлаждения дымовых газов до обычной температуры отработавших газов. Через отдельный выходной штуцер на противоположной стороне котла отработавшие газы выходят из котла.
Газовая горелка WM-G20 компании Weishaupt имеет компактное моноблоковое исполнение с наддувом и автоматическим режимом работы. В комплектацию горелки входят цифровой менеджер горения W-MF для управления запуском, контроля пламени и герметичности, а также электрическое управление шаговым электромотором для регулятора воздушного клапана и газового дросселя. Установлена необходимая газовая арматура для работы горелки.
Производимый парогенераторными установками пар используется для работы гранулятора. Гранулирование – технологический процесс выработки комбикормов, который заключается в преобразовании сыпучего мелкодисперсного продукта в частицы определенных размеров с заданными физическими свойствами. Гранулированию подвергаются рассыпные комбикорма для повышения эффективности их использования при кормлении животных. 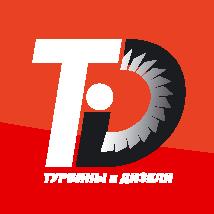