А. В. Таничев, В. В. Дурыманов, К. Р. Ишбулатова – ООО «Сименс»
А. Г. Степанов – ЗАО «Каспийский трубопроводный консорциум–Р»
В августе 2001 года были включены в работу семь газовых турбин для насосных перекачивающих станций (НПС) и произведен налив первого танкера в Новороссийске. Так начал функционировать 15007километровый нефтепровод Каспийского трубопроводного консорциума (КТК). Трубопровод протянулся от крупнейшего нефтяного месторождения Тенгиз (Казахстан) до г. Новороссийска. В качестве привода насосных агрегатов и электростанций в составе нефтепровода используются двигатели SGT-100 производства Siemens.
В августе 2001 года начал функционировать 1500-километровый нефтепровод Каспийского трубопроводного консорциума (КТК), который протянулся от крупнейшего нефтяного месторождения Тенгиз (Казахстан) до г. Новороссийска. Для перекачки нефти были задействованы семь магистральных насосов с двухвальным газотурбинным приводом и девять турбогенераторов. Приводами насосных агрегатов и электростанций являются двигатели SGT-100 производста Siemens .
В 2010 г. компания Siemens подписала контракт с Каспийским трубопроводным консорциумом на поставку дополнительных 11 насосных газотурбинных агрегатов на базе двухвальных газовых турбин SGT-100 мощностью 5,7 МВт и 4,9 МВт и насосов BFD производства Flowserve, а также на два турбогенератора. Они были поставлены для увеличения количества магистральных насосов на действующих НПС и строительства новых станций с магистральными насосами с турбинными приводами. В результате количество газотурбинных установок на текущих объектах КТК на территории России и Казахстана увеличилось почти вдвое. Таким образом, после завершения проекта расширения на территории России и Казахстана будут эксплуатироваться 18 магистральных турбонасосов и 10 турбогенераторов. Суммарная мощность газотурбинных установок КТК составит 146,4 МВт.
Трубопроводная система КТК – крупнейший на территории СНГ проект с участием иностранного капитала. В 2004 г. нефтепровод вышел на проектную мощность – 28 млн тонн в год. В настоящее время реализуется второй этап проекта – расширение Каспийской нефтепроводной системы. Это обусловлено тем, что изначально она разрабатывалась с учетом последующего повышения первоначальной пропускной способности до 67 млн тонн сырой нефти в год (в 2,5 раза).
Для достижения требуемой производительности ведется реконструкция существующих и строительство новых НПС с электроприводными и газотурбинными насосными агрегатами, а также модернизация существующих газотурбинных приводов магистральных насосов с увеличением мощности с 4,9 МВт до 5,7 МВт. Это уже на стадии предпроектной проработки и проведения тендеров поставило ряд сложных технических задач для заказчика, проектировщиков и поставщиков оборудования.
Компания Siemens активно включилась в данный процесс. Были тщательно изучены требования заказчика к характеристикам поставляемого оборудования и к его климатическому исполнению. Кроме того, проанализирован опыт эксплуатации агрегатов SGT-100, которые были поставлены для первого этапа предприятием в г. Линкольн (Великобритания). Такой подход позволил грамотно оценить возможности внедрения современных решений компании в существующее оборудование и найти оптимальный вариант, который мог бы устроить заказчика. В итоге КТК вновь остановил свой выбор на агрегатах SGT-100, прошедших стремительную эволюцию за 10 лет работы трубопроводной системы. Этого невозможно было бы достичь без потенциала совершенствования, заложенного в SGT-100.
Насосный агрегат на базе ГТУ SGT-100
Полнокомплектный модульный насосный агрегат SGT-100 включает турбоблок, насос с редуктором на раме, а также систему управления, маслосистему, модуль газового и жидкого топлива, системы выхлопа и всасывания воздуха, опорные конструкции и т.д.
Для перекачки сырой нефти в составе агрегата используется двухступенчатый центробежный насос BFD с горизонтальным разъемом корпуса, с рабочими колесами, расположенными симметрично (тип BB1 по API 610). Насос производства компании Flowserve, выполненный в соответствии с требованиями стандарта API 610, предназначен для сложных условий работы и обеспечивает перекачку жидкой среды с высокими значениями давления и расхода.
Приводом насоса служит газотурбинная установка SGT-100, которая поставляется для данного проекта в модификациях с номинальной мощностью 5,7 МВт и 4,9 МВт (ISO). Турбина имеет надежную, отработанную конструкцию, а также обладает высоким для агрегатов малой мощности КПД: 31,7…32,9 %. Одним из наиболее важных преимуществ SGT-100 является возможность ее поставки как в одновальном, так и двухвальном исполнении. Это позволяет одинаково успешно использовать ГТУ и для энергетических проектов, и в качестве механического привода. Согласно этому принципу обеспечена унификация энергетического и перекачивающего оборудования, эксплуатируемого КТК.
Новейшая версия газовой турбины SGT-100 – это 10-ступенчатый околозвуковой компрессор с консольной турбиной, показатели которого улучшены в результате постепенного совершенствования отдельных элементов конструкции. Такой подход позволил внедрить последние технологические новшества без ущерба для основных преимуществ платформы SGT-100, таких как надежность и эксплуатационная готовность.
Улучшенные характеристики компрессора достигнуты за счет использования осевого компрессора, конструкция которого аналогична компрессорам ГТУ для энергетического применения, обладающего самыми высокими на сегодня показателями. При этом использовалась технология трехмерного диффузионного аэродинамического проектирования. Повышение КПД турбины обеспечено за счет уменьшения перетекания потока между ступенями и улучшенной организации охлаждения лопаток первой ступени турбины.
Необходимо отметить, что вновь поставленные агрегаты (наравне с эксплуатируемыми) оснащены двухтопливной системой, обеспечивающей работу как на газовом, так и на жидком топливе, что позволяет продолжить перекачку нефти в случае перебоев с одним из видов горючего. При этом переход с главного газового топлива на дизельное топливо производится автоматически, с предупреждающей фиксацией системами управления ГТУ возникших проблем.
Камера сгорания DLE
Общеизвестно, что одним из важнейших показателей совершенства современных ГТУ является уровень выбросов в атмосферу. Обеспечение жестких нормативов по выбросам NOx и СО становится одним из основных факторов в эксплуатации объектов энергетики.
Высокие экологические показатели ГТУ достигаются благодаря использованию новейших технологий организации рабочего процесса в камере сгорания. В КС реализуется технология горения бедной гомогенной смеси с поддержанием в зоне горения определенной температуры пламени. Такая технология (DLE) применяется не только на вновь поставленных агрегатах, но и на существующих, обеспечивая низкие уровни эмиссии NOx и СО (менее 25 ppm).
Особенностью технологии DLE является использование горелки, в которой сжигается предварительно подготовленная обедненная смесь. Горелка, служащая для подготовки однородной топливовоздушной смеси, представляет собой шайбу-завихритель с подачей топлива непосредственно в завихритель через множественные каналы между его лопатками. Для розжига КС при запуске и предотвращения срыва пламени на переходных режимах небольшое количество топлива постоянно подается в пилотную горелку, расположенную по центру шайбы-завихрителя. Запальная свеча, работающая только на запуске, выведена на поверхность пилотной горелки.
Закрученный поток имеет настолько высокую скорость, что процесс сжигания не может начаться внутри собственно завихрителя. Кроме того, завихрение потока вызывает его рециркуляцию в КС, в результате чего на выходе завихрителя возникает зона обратных токов. Устойчивость сжигания в этой зоне обеспечивается низкой скоростью и высокой турбулентностью.
Таким образом, в камере сгорания реализуется равномерное поле температур, способствующее максимальному сгоранию смеси с минимальными выбросами. При этом система регулирования расхода вторичного воздуха на частичной нагрузке обеспечивает оптимальный состав топливной смеси на различных режимах работы ГТУ. Как результат, турбина SGT-100 имеет низкие показатели выбросов в максимально широком диапазоне рабочих режимов.
Компоновка агрегата
Изменения коснулись не только газотурбинной установки и центробежного насоса – компоновка агрегата также претерпела ряд существенных изменений. В частности, была применена модульная конструкция отдельных вспомогательных систем агрегата, что позволяет производить их легкую замену и монтаж. Кроме того, большая часть этих модулей, устанавливаемых ранее вне агрегата, перенесена на раму турбоблока, включая модули подачи газового и жидкого топлива, продувки жидкого топлива и др. Существенно уменьшилось количество металлоконструкций. Все это делает агрегат максимально компактным. При поставке также учтены климатические условия эксплуатации оборудования.
Таким образом, можно сделать вывод: компания Siemens производит сегодня высококонкурентный продукт – агрегат SGT-100, обладающий приемлемой ценой, надежностью, удовлетворяющий современным требованиям безопасности, эффективности и экологичности.
Организация технической поддержки
Персонал Siemens, обслуживающий турбины КТК, в т.ч. и постоянно проживающий на территории России, имеет самую высокую квалификацию и наибольший опыт обслуживания турбин SGT-100, владеет всеми технологиями по обслуживанию, регулировкам и настройкам и может гарантировать полноту и качество технического обслуживания во всем спектре работ. Время оперативного реагирования на проблемы, возникающие на объектах КТК, – не более 24 часов. Siemens имеет возможность для удаленного мониторинга основных параметров работы турбин. Профессиональная группа технической поддержки на заводе-изготовителе выдает оперативные рекомендации обслуживающему персоналу КТК по возникающим в процессе эксплуатации вопросам.
В результате заказчик может рассчитывать на высокий уровень компетенции и на возможности локальной сервисной организации Siemens, включая российскую команду инженеров по эксплуатации и ремонту, сервисный центр, расположенный в г. Краснодаре, недалеко от объектов КТК. Учитываются также преимущества действующего долгосрочного договора на техническое обслуживание имеющихся на данный момент агрегатов, а также новых, ввод в эксплуатацию которых планируется в течение 2013–2014 гг.
Достигнутый в настоящее время технический уровень газотурбинных технологий в сочетании с автоматизацией основных технологических режимов позволяет минимизировать риск незапланированных простоев оборудования, существенно снижающих его экономические показатели. Очевидно, что этого можно добиться только при реализации продуманной концепции технического обслуживания энергетического оборудования на протяжении всего жизненного цикла.
Современная концепция технической поддержки эксплуатации ГТУ предполагает, что если соблюдать рекомендованный изготовителем регламент обслуживания, то можно свести к минимуму риск возникновения нештатных ситуаций и, соответственно, внеплановых ремонтов. Таким образом, вопросы технической поддержки можно разделить на две основные группы:
1. Регламент и стоимость планового технического обслуживания;
2. Организационная составляющая технической поддержки.
Регламент технического обслуживания представляет собой определенный производителем комплекс обязательных для исполнения (по объемам и срокам) плановых работ. В соответствии с ним определяется объем необходимых запасных частей и трудоемкость работ, а это, в свою очередь, непосредственно влияет на время плановых простоев ГТУ и стоимость планового технического обслуживания. Последний показатель можно оценить по удельной стоимости плановых инспекций/ ремонтов за жизненный цикл ГТУ (обычно от 100 до 120 тыс. часов). Этот показатель включает в себя стоимость работ, запасных частей для всех видов планового обслуживания (включая капитальные ремонты), а также необходимые для проведения работ инструменты.
Деятельность сервисных центров Siemens включает профилактическое (плановое) обслуживание, направленное на поддержание оборудования в исправном состоянии и предупреждение аварийных ситуаций, и корректирующее (внеплановое), ориентированное на быструю ликвидацию возникших неполадок и их последствий. Цель сервисной поддержки заказчика – оптимизация профилактического обслуживания, сводящая к минимуму время внеплановых простоев оборудования.
Основным инструментом, определяющим комплекс мероприятий, является долгосрочный сервисный договор между заказчиком и компанией (региональным сервисным центром). Заказчику предлагается на выбор несколько уровней договоров, которые отличаются объемом оказываемых услуг и степенью вовлеченности компании в процесс эксплуатации и обслуживания оборудования.
Продолжительная практика сервисных соглашений доказала их целесообразность за рубежом. В России такие виды договоров применяются редко в связи с отсутствием долгосрочного планирования бюджета. Несмотря на это, все чаще долгосрочные соглашения на техническое обслуживание заключаются совместно с договором на поставку нового оборудования. Долгосрочный договор, как правило, заключается на срок от 5 до 15 лет. Детальная разработка программы обслуживания проводится в тесном сотрудничестве с заказчиком, чтобы максимально учесть специфику оборудования, условия и режимы его работы. Досконально проработанные сервисные договоры обеспечат не только соответствие требованиям по эксплуатации оборудования, но и минимизируют затраты на его обслуживание.
Долгосрочный контракт на обслуживание
Начиная с 2005 г. компания Siemens осуществляет долгосрочную сервисную поддержку агрегатов, поставленных для КТК. В 2009 г. с консорциумом был заключен очередной долгосрочный контракт на обслуживание 15 агрегатов на базе газовых турбин SGT-100, в 2012 г. подписано дополнение к договору, в рамках которого все новые агрегаты проекта расширения также будут включаться в объем долгосрочного контракта на обслуживание. В итоге Siemens будет обслуживать на территории России и Казахстана 18 магистральных турбонасосов, 6 основных и 4 резервных (МТ, НПС «Атырау») турбогенератора, т.е. в общей сложности 28 газотурбинных агрегатов на базе SGT-100.
Контракт включает плановые и внеплановые работы на агрегатах и обслуживание насосов. Siemens вместе со своим подрядчиком по насосам может выполнить все работы по внеплановому техническому обслуживанию и планово-предупредительному ремонту.
Планово-предупредительный ремонт на объектах КТК выполняется в ходе проведения инспекций – A (после 8000 EOH), B (после 24000 ЕОН) и C (после 48000 ЕОН). В рамках сервисного договора компания оказывает КТК целый комплекс услуг, включая (но не ограничиваясь):
• планирование и проведение инспекций оборудования согласно разработанному совместно с КТК графику;
• постоянный мониторинг рабочих параметров и анализ состояния оборудования при помощи удаленной системы мониторинга;
• аварийные выезды специалистов;
• консультационную поддержку, включая рекомендации по решению возникших технических проблем;
• выработку рекомендаций по совершенствованию системы очистки воздуха с применением фильтров HEPA, включая анализ отложений на фильтроэлементах воздухоочистительного устройства;
• оперативное реагирование на вызовы, включая проведение сложных металлографических анализов лопаток дисков высокого давления, позволяющих точно оценить состояние турбин и скорректировать назначенный ресурс исходя из условий работы ГТУ;
• круглосуточную телефонную поддержку на русском языке;
• обучение обслуживающего персонала;
• рекомендации по замене частей узлов оборудования и его модернизации;
• поставку (плановую и срочную) запасных частей и расходных материалов;
• всестороннюю поддержку при возникновении нештатных ситуаций (выезд квалифицированного персонала для выяснения причины и устранения неполадок, координация работ и пр.).
Такая организация сервисной поддержки позволяет Siemens соответствовать коммерческим интересам заказчика, где приоритетами являются бесперебойная работа оборудования, оптимизация расходов на эксплуатацию, заранее планируемое распределение затрат на обслуживание в продолжение всего жизненного цикла оборудования и т.д.
Компания Siemens имеет в своем штате российских высококвалифицированных инженеров по эксплуатации и ремонту турбин малой мощности (SGT): девять из них стратегически базируются в Краснодаре, один инженер находится в Новороссийске. Компания также располагает службой технической поддержки в Москве. В рамках долгосрочного договора Siemens периодически командирует постоянного представителя завода-изготовителя на объекты КТК, который контролирует текущее состояние оборудования.
На предприятии Siemens в г. Линкольн работают 15 обученных специалистов, имеющих российские и казахстанские визы. При необходимости они оказывают помощь в устранении неполадок на нефтепроводе.
Плановое и корректирующее обслуживание
Программы технического обслуживания ГТУ и вспомогательных систем представляют собой установленный порядок проведения необходимого комплекса работ в зависимости от времени эксплуатации.
Учитывая, что готовность энергоустановки определяется продолжительностью как вынужденных, так и плановых простоев, необходимо использовать время таких простоев с максимальной эффективностью. В связи с этим программа техобслуживания предусматривает проведение работ во время плановых остановов в тесной координации с заказчиком. Технические работы, выполняемые в соответствии с программой планового обслуживания, основаны на уровневой системе – инспекциях A, B и C.
Интервалы времени, через которые необходимо проводить соответствующее обслуживание, определяются не только количеством часов наработки турбины, но и эксплуатационными факторами – нагрузка, количество пусков, тип и качество используемого топлива. Для этого применяется комплексный показатель – эквивалентное время наработки (эквивалентные часы). Пример расчета эквивалентных часов наработки приведен на рис. 5. Все работы по плановому техобслуживанию проводятся только специально подготовленным, высококвалифицированным персоналом компании. По окончании каждой технической инспекции заказчику выдается отчет с результатами инспекции и рекомендациями по дальнейшей эксплуатации и обслуживанию.
Корректирующее техобслуживание проводится в случае появления особых обстоятельств, в том числе нештатных ситуаций. В таких случаях сервисные центры компании готовы предложить заказчикам полную поддержку – начиная с рекомендаций по выявлению неисправностей и срочного выезда технического персонала и заканчивая срочной доставкой запчастей и выполнением ремонтных работ.
Для успешной реализации корректирующего обслуживания необходимо наличие на площадке требуемых инструментов, запчастей и специальной оснастки (приспособлений) для проведения работ.
Запасные части
Наличие запчастей и расходных материалов на площадке проведения работ имеет важное значение при обслуживании оборудования как во время эксплуатации, так и при проведении ремонтов.
Запасные части и расходные материалы в зависимости от назначения делятся на три основные группы:
• для эксплуатации – покрывают потребности оперативного (постоянного) обслуживания оборудования и поддержания его в высокой степени готовности (рекомендуются для формирования склада на площадке);
• для планового обслуживания – предназначены для плановых замен во время выполнения инспекций (необходимы на площадке к началу проведения инспекций);
• для капитальных ремонтов – представляют собой дорогостоящие сложные компоненты/модули оборудования (могут поставляться со склада завода-изготовителя или регионального сервисного центра).
Региональные сервисные центры Siemens совместно с заказчиками разрабатывают программу плановых поставок материалов на площадку для создания склада. Такой подход позволяет заказчику заранее планировать бюджет на «актуальный» период.
Сервисная организация Siemens в России
Реализация концепции сервисной поддержки является для заказчика эффективным вложением средств. Компания Siemens в России оказывает поддержку таким крупным компаниям, как ОАО «Газпром», ОАО «Роснефть», Каспийский трубопроводный консорциум–Р, корпорация «ТВЭЛ», ООО «Объединенные пивоварни Хейнекен», компания «Тоталь разведка разработка Россия», ОАО «Уралкалий», ОАО «ЛУКойл». Число заказчиков увеличивается с каждым годом.
Центральный офис российского сервисного отделения Siemens находится в Москве и координирует все мероприятия по техобслуживанию промышленных ГТУ в сотрудничестве с сервисными службами заводов-изготовителей в Швеции, Великобритании, Чехии, Германии, США. Также отдел выполняет плановые и внеплановые поставки узлов оборудования с полным документальным оформлением, позволяя заказчику максимально сокращать сроки и собственные затраты.
В 2005 г. российским подразделением компании образован сервисный центр в г. Краснодаре. Его создание и локализация были ориентированы, в первую очередь, на потребности Каспийского трубопроводного консорциума – одного из крупнейших заказчиков газотурбинных установок Siemens малой мощности в России. Сервисный центр многофункционален и проводит инспекции газовых турбин малой мощности SGT-100 с заменой деталей и узлов ГТУ, а также хранение запчастей, компонентов турбин, вспомогательных систем и долгосрочное хранение турбинных агрегатов.
Производственная площадь предприятия составляет 420 м2. Оно оснащено необходимым подъемным оборудованием, инструментом для проведения механосборочных работ, спецприспособлениями и оснасткой. Силами технического персонала компании проводятся инспекции уровня B и восстановительные ремонты на двигателях SGT-100.
Возможности Краснодарского сервисного центра вместе с сервисным отделом в Москве позволяют компании Siemens предлагать российским заказчикам полный спектр услуг в процессе эксплуатации оборудования. Благодаря опыту, накопленному при эксплуатации агрегатов КТК, привлечение компании к работам по вводу поставленного оборудования в эксплуатацию, несомненно, обеспечит высокий уровень надежности системы в будущем. 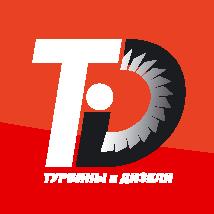