М. Р. Гасуль – ОАО "НПО "Сатурн"", г. Рыбинск
Разработка газотурбинной энергетической установки ГТЭ-110 началась в 1991 году по заказу РАО «ЕЭС России». В декабре 2003 г. установка на базе ГТД-110 №2 в составе испытательного стенда Ивановских ПГУ прошла межведомственные испытания.
В 2004 г. в ОАО «НПО «Сатурн» начато серийное производство и к настоящему времени изготовлено 6 установок ГТЭ-110.
Опыт эксплуатации ГТЭ в парогазовом цикле выявил ряд дефектов, которые не проявлялись при испытаниях и доводке установки в составе испытательного стенда. К сожалению, отсутствие технологического двигателя для опробования существенно сдерживало внедрение мероприятий по устранению выявленных дефектов. Разработанные мероприятия зачастую внедрялись в серию без соответствующей проверки и испытаний в составе технологического ГТД.
В период с 2007 по 2013 гг. НПО «Сатурн» совместно с ведущими экспертами отрасли проводило работы по определению возможностей модернизации ГТД-110. В результате разработано предварительное технико-экономическое обоснование проекта по созданию модернизированной газовой турбины ГТД-110М.
Газотурбинный двигатель ГТД-110М – однокаскадный, с двухопорным ротором, простого термодинамического цикла, с отбором мощности со стороны компрессора. Двигатель устанавливается на раме. Компрессор – осевой, 15-ступенчатый, с регулируемым входным направляющим аппаратом (ВНА). Камера сгорания – трубчато-кольцевая, с двадцатью жаровыми трубами. Турбина – 4-ступенчатая, с охлаждаемыми сопловыми и рабочими лопатками первой и второй ступеней.
Предварительно для создания модернизированного ГТД-110М согласно ISO установлены такие значения: номинальная мощность 118,6 МВт, коэффициент полезного действия 36 %. Ресурс между капитальными ремонтами 25 000 часов при числе пусков не более 300, назначенный ресурс – 100 000 при числе пусков не более 1000.
В качестве целевой характеристики узлов, деталей механизмов установлен комплексный целевой показатель: ресурс между капитальными ремонтами – 25 000 эквивалентных часов с промежуточными периодическими инспекциями. Для обеспечения надежности при длительной эксплуатации изменены отдельные узлы.
Ресурсная камера сгорания
По результатам эксплуатации и предложенным мероприятиям по устранению дефектов была разработана конструкция ресурсной камеры сгорания. Три опытные жаровые трубы новой конструкции (рис. 1б) на 16.10.2015 наработали в составе ГТД-110 10607 экв. часов и продолжают эксплуатироваться в составе двигателя № 4. На ГТД №3 и №4 установлены комплекты разъемных жаровых труб (20 шт. на изделие), наработка в эксплуатации лидерного комплекта составляет 7911 экв. часов. Остальные двигатели будут доработаны при проведении ремонтов.
Разработана и внедрена в эксплуатацию новая конструкция патрубков пламяпереброса с увеличенным зазором (рис. 2). В течение 2011–14 гг. дефектов патрубков пламяпереброса отмечено не было.
С целью улучшения теплового состояния жаровой трубы разработана конструкция патрубков пламяпереброса с плавающей муфтой – опытные образцы патрубков (3 шт.) работают в составе ГТД-110 № 4.
Рабочая лопатка 1-й ступени
При эксплуатации двигателей ГТД-110 неоднократно отмечены случаи разрушения рабочих лопаток турбины в замковой части, имеющие усталостный характер и вызванные накоплением повреждаемости при прохождении резонансных режимов на запуске двигателя. Для устранения дефекта в эксплуатации внедрены следующие мероприятия:
1. Изменения динамических характеристик рабочей лопатки. Для этого выполнена подрезка выходной кромки пера по всей высоте. Мероприятие внедрено на двигателях № 4 (февраль 2013 г.) и № 3 (март 2015 г.).
Для устранения термоусталостных трещин на периферийной части лопаток в зоне наплавки и пылеотводящих отверстий изменена конструкция реборды лопатки. От наплавки отказались, реборда формируется в отливке. Эффективность решения проверяется на ГТД № 3, остальные двигатели будут доработаны при ремонте.
2. Изменение конструкции замкового соединения рабочей лопатки и диска. Для ограничения амплитуды колебания рабочей лопатки и увеличения жесткости в зоне удлинительной ножки введены «приливы», по аналогии с конструкцией рабочей лопатки 2-й ступени.
Для того чтобы компенсировать разницу коэффициентов теплового расширения материалов рабочей лопатки и диска, изменен шаг зубьев замка рабочей лопатки на 25 мкм, суммарное изменение 50 мкм. Мероприятия внедрены на ГТД № 3 в марте 2015 г., остальные двигатели будут доработаны при ремонте.
3. Увеличение осевого зазора между сопловыми и рабочими лопатками 1-й ступени турбин. Учитывая малое осевое расстояние между сопловым аппаратом и рабочей лопаткой 1-й ступени, выполнена подрезка сопловых лопаток по выходной кромке (рис. 3), чтобы снизить уровень возмущающего динамического воздействия на рабочую лопатку. Меропри-ятие внедрено на ГТД № 3 и № 4, наработка более 4000 экв. часов, остальные двигатели будут доработаны при ремонте.
Чтобы еще больше увеличить осевое расстояние между сопловым аппаратом и рабочей лопаткой 1-й ступени, планируется сместить сопловой аппарат 1-й ступени на 15 мм в сторону камеры сгорания. Проверка эффективности данного мероприятия запланирована на двигателе № 2 в III квартале 2016 г.
4. Применение демпфера. В конструкцию вводится подполочный демпфер сухого трения – это должно снизить динамические напряжения в замковой части за счет диссипации энергии и изменения частотных характеристик рабочей лопатки. Опытные лопатки с демпфером планируется испытать на двигателе № 2 во II квартале 2016 г.
5. Изменение оребрения внутренней части канала охлаждения. Для снижения градиента температур и устранения термоусталостных трещин в зоне входной кромки, согласно тепловым и гидравлическим расчетам, целесообразно убрать оребрение кромочного канала охлаждения на высоте 15 мм от трактообразующей полки. Опытные работы возможны после изменения конструкции стержня, изготовление опытных образцов запланировано на I квартал 2017 г.
6. Изменение трактообразующей полки. Чтобы устранить термоусталостные трещины на трактообразующей полке, в зоне входной кромки вводится радиусный переход полки в боковую стенку кармана по аналогии с конструкцией рабочей лопатки 2-й ступени, увеличивается толщина полки, выполняется перфорация. Изготовление опытных образцов запланировано на I квартал 2017 г.
7. Изменение количества лопаток соплового аппарата 1- и 2-й ступеней. Это позволяет изменить наиболее неблагоприятные 40- и 48-ю гармоники, снизить уровни возбуждения рабочей лопатки 1-й ступени. Доработку ГТД № 2 планируется выполнить после завершения первого этапа испытаний в 2016 г.
Трубопроводы внешних коммуникаций ГТД
Разработана компоновка с применением сильфонных компенсаторов на трубопроводах охлаждающего воздуха, готовится рабочая конструкторская документация. Определен поставщик теплообменника для системы охлаждения турбины, оформляется договор поставки. Испытания выносного теплообменника и всей системы в составе ГТД-110 № 2 запланированы на 2016 г.
Создание малоэмиссионной камеры сгорания
Работы по созданию малоэмиссионной камеры сгорания проводятся совместно с ВТИ и ЦИАМ им. П.И. Баранова. В течение октября 2015 г. проведена серия испытаний в ЦИАМ на стенде полных параметров Ц17 в составе одногорелочного отсека. По результатам испытаний в ноябре 2015 г. будет проведен НТС с выбором наиболее подходящего варианта малоэмиссионной камеры сгорания для испытаний в составе ГТД № 2.
Прогноз рынка энергетических ГТУ мощностью 100…180 МВт
Согласно прогнозам отдела маркетинга НПО «Сатурн», развитие мирового и отечественного рынка ГТД большой мощности идет в сторону увеличения единичной мощности двигателей. Для удовлетворения потребности рынка в энергетических ГТД большой мощности предприятие предлагает расширить модельный ряд ГТД-110М до 135 МВт.
Мощность двигателя 125, 130 и 135 МВт достигается увеличением расхода воздуха на входе в компрессор на 3–5 % за счет раскрытия угла ВНА до +5°, в существующей геометрии, с КПД компрессора 0,86 и КПД турбины 0,92, степенью повышения давления 15,8, а также с одновременным повышением температуры отработавших в турбине газов до 530, 540 и 550 °С соответственно. На рис. 4 показана зависимость мощности ПГУ от мощности двигателя.
Для сохранения исходного материала рабочих лопаток 1-й ступени (ЧС88У-ВИ) для варианта мощностью 125 МВт необходима оптимизация схемы их охлаждения (новый воздухоохладитель). Для вариантов 130 и 135 МВт нужна полная модернизация схемы охлаждения рабочих лопаток, а также применение новых жаропрочных сплавов, включающих редкоземельные элементы – Рений, Тантал и Рутений, работоспособных при температурах не менее 1050 °С.
Выводы
1. В России имеются все необходимые условия для начала развития газотурбинной энергетики большой мощности (децентрализация /либерализация энергетической отрасли, дешевый газ, развивающаяся сеть трубопроводов, необходимость скорейшей модернизации энергетической отрасли и др.).
2. Сегмент рынка энергетических ГТД в классе мощности 100…130 МВт очень узкий (около 6 %). Создание машины в сегменте мощности 130…180 МВт позволит значительно расширить рынок ГТД-110/180 (до 25 %).
3. НПО «Сатурн» рекомендует подготовить проект ТЗ по одному из предложенных вариантов модернизации двигателя ГТД-110М.
4. НПО «Сатурн» рекомендует начать поиски потенциального заказчика данной работы. 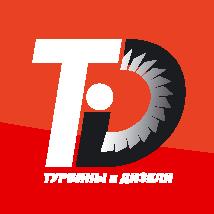