К. А. Виноградов (к.т.н.), И. С. Добровольский, К. Р. Пятунин, В. П. Крупин, С. М. Пиотух – ПАО «ОДК–Сатурн»
Эффективность использования ГТД в качестве привода электрогенератора на электростанции или для других целей напрямую зависит от КПД газотурбинного двигателя и энергоустановки в целом.
Один из основных путей повышения эффективности ГТД и энергоустановок на их основе – увеличение температуры газа перед турбиной. При этом для наземных двигателей важнейшую роль в обеспечении эффективной работы играет ресурс деталей и узлов ГТД. Такие элементы горячей части двигателя, как рабочие лопатки и диск первой ступени турбины, работают в наиболее сложных условиях (по температурам и испытываемым нагрузкам), являясь основными с точки зрения обеспечения высоких значений температуры газа перед турбиной, а также требуемого ресурса двигателя и установки в целом.
Наиболее простой и естественный путь освоения области высокой температуры газа перед турбиной – использовать для изготовления элементов турбин материалы, способные выдерживать такие температуры и большие напряжения в течение заданного срока службы. Однако темпы роста допустимой температуры металла, обусловленные совершенствованием материалов, отставали и отстают от темпов роста температуры газа.
Все эти факторы подчеркивают важность разработки высокоэффективной системы охлаждения для основных элементов турбины (лопатки и диски первых ступеней), что требует корректного моделирования процессов, происходящих в ней при проектировании и доработке системы.
При этом использование методов численной газовой динамики (CFD) для моделирования процессов в системе охлаждения турбины (охлаждение лопаток СА и РК, течение в системе подвода охлаждающего воздуха и т.д.) позволяет решить данную задачу. Ключевым фактором применимости данного подхода является получаемая точность моделирования, а также временные затраты на построение модели и проведение расчетов. Для получения приемлемого по точности результата необходимо выполнять верификацию используемой модели по экспериментальным данным.
Цель данной работы – разработать численную модель, корректно описывающую тепловое состояние основных элементов СА и РК 1-й ступени турбины, а также процессов, происходящих в системе охлаждения РЛ и диска 1-й ступени, в смежных полостях и в проточной части турбины ГТД-110 (фото).
Получить корректную модель процессов, происходящих в системе охлаждения, путем гидравлического и теплового расчета полостей системы охлаждения и внутренних каналов лопатки с помощью последовательных приближений с последующим заданием коэффициентов теплоотдачи через критериальные уравнения – достаточно сложно. Модель теплового состояния и гидравлических характеристик такой сложной системы, как РК 1-й ступени турбины и прилегающих полостей, должна учитывать влияние различных факторов (параметры режима, зазоры в лабиринтных уплотнениях) на особенности течения в системе, на тепловое состояние основных деталей и эффективность работы системы.
Для построения модели сопряженного теплообмена и гидравлических характеристик авторами была создана 3D-модель сборки деталей рабочего колеса (лопатка, диск, сегменты) в горячем состоянии (с учетом изменения радиальных зазоров на режиме и теплового расширения деталей). Расчетная область включает: систему подвода охлаждающего воздуха к РЛ, РЛ 1-й ступени и диск, герметизирующие сегменты, полости после и перед РК 1-й ступени, а также проточную часть. Общий вид расчетной модели РК 1-й ступени приведен на рис. 1.
В данном случае моделируется течение в системе подвода охлаждающего воздуха, что обеспечивает корректное описание структуры и параметров потока в междисковой полости подвода воздуха к РК (учет вихревого течения в полости подвода воздуха). Также моделируется течение в слабовентилируемых полостях перед РК, течение в полостях в замковом соединении лопатки, диска и герметизирующих сегментов, течение во внутренней полости РЛ. Одновременно с этим моделировалось течение в проточной части турбины, что вызывает дополнительные трудности при расчетах из-за большой разницы в скоростях потока. При этом по внутренним и наружным поверхностям лопатки, замкового паза, герметизирующих сегментов было задано граничное условие сопряженного теплообмена.
Особое внимание при разработке данной модели было уделено течению и теплообмену в замковом соединении: смоделированы перетечки в пазах замка, распределение воздуха на охлаждение РЛ и продувку пазов, а также утечки через отверстия в герметизирующих сегментах.
Расчетная сетка металла лопатки, диска и герметизирующих сегментов, а также расчетная сетка газа и охлаждающего воздуха была построена в ПК ICEM CFD 17. В среде газа и воздуха использовалась неструктурированная тетраэдрическая сетка с призматическими слоями, в металле – тетраэдрическая сетка. Сетки были выполнены по технологии, обеспечивающей стыковку «узел в узел». Общее число узлов расчетной сетки составило 42 млн. Расчеты выполнялись в программном комплексе ANSYS CFX 17.
Для определения теплового состояния и гидравлических характеристик использовался прямой метод сопряженного теплообмена (Conjugate heat transfer), реализованный в программном комплексе ANSYS CFX 17. При данном подходе в металле решается уравнение теплового баланса, полученное в соответствии с принципом сохранения энергии, для дискретизации которого используется метод конечных элементов. Течение вязкой сжимаемой жидкости описывается осредненными по времени уравнениями Навье-Стокса, замкнутыми при помощи той или иной модели турбулентности. Авторами использовалась модель турбулентности SST (Shear Stress Transport), верифицированная в ПАО «ОДК–Сатурн» для решения данного типа задач.
В ходе работ по настройке модели выполнены верификационные расчеты в условиях пакетного стенда, по результатам которых можно сделать вывод, что основные процессы теплообмена в лопатке такой размерности моделируются корректно.
Результаты расчетов на режиме двигателя сравнивались с экспериментальными данными по температурам в смежных полостях при термометривании в 2013 г.
Также выполнены верификационные расчеты для сравнения с результатами термометрирования рабочей лопатки в 2016 г. Выявлено согласование характеристик теплового состояния РЛ 1-й ступени, полученных в ходе экспериментальных исследований и при проведении численного моделирования режимов термометрирования, и штатных номинальных режимов работы ГТД.
На рис. 2 приведено сравнение расчетной и экспериментальной эффективности охлаждения среднего сечения рабочей лопатки:
Θ = (TГ – TЛ)/(TГ – TВ). (1)
Видно, что расчетная эффективность охлаждения находится в диапазоне значений, полученных при термометрировании на двигателе. Отклонение от эксперимента составляет ΔΘ = 0,01…0,04 в зависимости от области профиля, что говорит о корректности моделирования теплогидравлических характеристик с помощью разработанной модели.
На рис. 3 приведены результаты расчета исходного варианта системы охлаждения РК 1-й ступени турбины: структура потока в меридиональном сечении расчетной области, тепловое состояние замковой части лопатки, распределение температуры по линиям тока вокруг замка и ножки лопатки.
С использованием разработанной численной модели были выполнены сравнительные расчеты теплового состояния различных вариантов системы охлаждения РЛ, принято решение о внедрении модернизированной рабочей лопатки в конструкцию двигателя.
Существенный объем расчетных работ был выполнен и для соплового аппарата (СА) 1-й ступени. В рамках работ по повышению эффективности охлаждения трактовых полок СА 1-й ступени разработан ряд расчетных моделей для оценки теплового состояния трактовых полок. При разработке моделей использовались программные комплексы NUMECA (построение расчетной сетки для газодинамических расчетов, выполнение расчетов в упрощенной постановке) и ANSYS CFX (поверочные газодинамические расчеты с моделированием отверстий перфорации с помощью «колодцев» на трактовой полке).
Как влияют расположение и характеристики отверстий перфорации на торцевых поверхностях СА на тепловое состояние полок и лопатки, оценивалось с помощью 3D-модели сопряженного теплообмена СА 1-й ступени в программном комплексе ANSYS CFX 17. Общий вид расчетной модели на рис. 4.
С использованием разработанных моделей газодинамических расчетов выполнены расчеты трех вариантов расположения отверстий перфорации на трактовой полке СА (исходный вариант и два модернизированных варианта), проанализированы картины течения, выполнено сравнение эффективности охлаждения трактовых полок.
По результатам расчетов выявлены зоны с низкой эффективностью пленочного охлаждения. Например, к таким зонам можно отнести область трактовой полки вблизи корыта лопатки. Это связано с влиянием вторичных течений на торцевой стенке, сдувающих незакрученную часть охладителя поперек канала, что приводит к усилению охлаждения вблизи спинки профиля и снижению охлаждения вблизи корыта.
Как показывают исследования [1–3], эффективность пленочного охлаждения (1) можно повысить, заменив традиционные цилиндрические отверстия перфорации веерными (рис. 5). Особенностью последних является наличие диффузорного участка на выходе из отверстия, что позволяет избежать отрыва струи охладителя от поверхности и обеспечить более равномерное охлаждение.
На рис. 6 приведено сравнение эффективности охлаждения, осредненной по длине средней линии трактовой полки, для трех вариантов отверстий перфорации. На рис. 7 дано сравнение температуры поверхности для исходного и оптимизированного (с веерными отверстиями) варианта системы пленочного охлаждения трактовых поверхностей.
Помимо увеличения площади и равномерности охлаждения, при использовании веерных отверстий перфорации эффективность пленочного охлаждения, осредненная вдоль средней линии трактовой полки, повысилась на 20 % по сравнению с исходным вариантом системы охлаждения.
Верификация результатов, полученных на численной модели, проводилась по данным литературных источников и экспериментальных исследований, выполненных на пакетном стенде, а также с учетом термометрирования СА 1-й ступени непосредственно на двигателе.
В рамках совершенствования конструкции были подобраны необходимые углы наклона отверстий, количество рядов перфорации, параметры выдува. Результаты оценочных расчетов для исходного и оптимального вариантов интегрированы в расчетные модели сопряженного теплообмена СА 1-й ступени, где подтвердилась эффективность предложенного варианта расположения отверстий.
В результате, разработанная расчетная трехмерная модель позволила оптимизировать расположение отверстий пленочного охлаждения на трактовых полках сопловых аппаратов, сравнивать эффективность различных вариантов конструкций и рекомендовать оптимальный вариант схемы охлаждения СА.
Таким образом, созданная трехмерная модель теплогидравлических характеристик 1-й ступени турбины ГТД-110 позволяет эффективно решать следующие задачи:
- оценивать тепловое состояние и эффективность охлаждения основных деталей, а также особенности течения в системе охлаждения 1-й ступени;
- учитывать и анализировать влияние различных факторов (геометрические, режимные параметры) на характеристики системы, выполнять сравнительную оценку мероприятий по повышению эффективности охлаждения основных элементов СА и РК 1-ступени;
- проводить верификацию и настройку 1D и 2D гидравлических и тепловых моделей для подобного класса задач.
Результаты расчета теплогидравлических характеристик, полученные на данной модели, используются на предприятии «ОДК–Сатурн» при прочностном и ресурсном анализе конструкции турбины, а также при принятии решений о модернизации элементов существующей системы охлаждения. 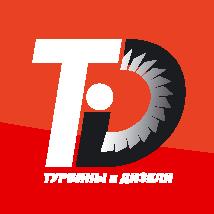